Self Made Knives
Well-Known Member
A knife maker's vise is probably already on your bench if you've been doing this for very long, but for my fellow newbies, I documented building mine. Maybe it'll help somebody or give you some ideas for your own design. I shot a lot of video too, so I'll post a link to a YouTube video when I'm finished editing it.
First off, this is how I've been doing it so far, and it kind of stunk! I'd clamp blades in a bench vise or add a little vise on top of that, but I was still very limited in work positions.
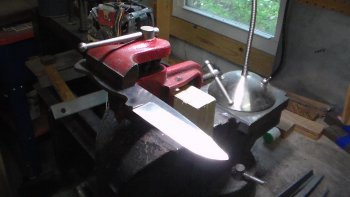
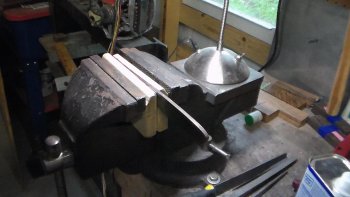
So, I started off with two pieces of stainless pipe, fairly thick walled. The tubes have about an 1/8" gap, which worked ok, but the tighter fit you get here, the better they'll clamp down without rocking.
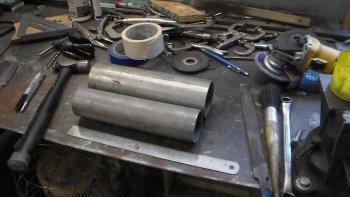
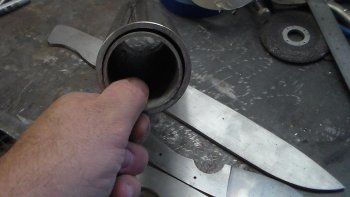
My inner tube has an i.d. of 2.125", which should handle any knife I foresee myself making. Here's a typical smaller blade and a 2" wide blade inserted.
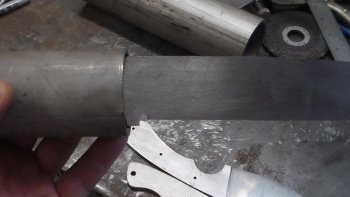
Using a piece of angle, scribe a straight line on your smaller tubing and drill and tap a hole on each end. I chose tapping my holes instead of welding nuts on the outside, in case I ever want to take it apart again.
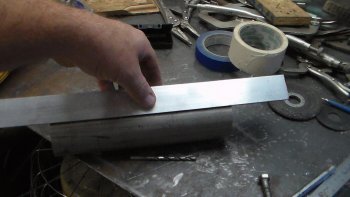
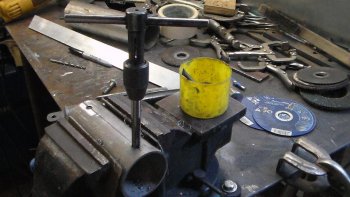
Word of caution here on your design. I'm bad about designing on the fly and made my inner tube 4.75" long and the holes are tapped very close to the ends. I wish I'd made it at least 5" wide. As you'll see later, I made some T-bolts for my clamp screws and if I spin the vise all the way over upside down, the knobs on the T-bolts sometimes interfere with the base. Not a big deal, but just a little extra length would've prevented it.
I wrestled around with how I wanted the inner vise jaws to operate. I knew the top jaw would be fixed to the T-bolts and the same length as the inner tube, but the bottom jaw(s) could be fixed, floating, short, long, etc. I decided on a floating jaw, that would be captured in the vise with notches, but could be easily lifted out and flipped end for end.
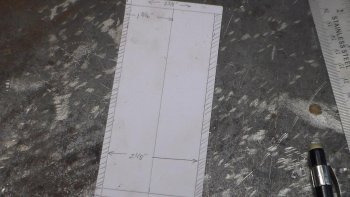
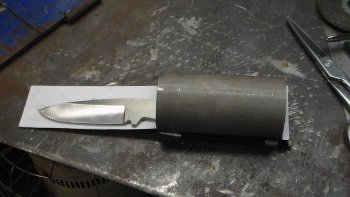
Stay tuned, more to come.......
First off, this is how I've been doing it so far, and it kind of stunk! I'd clamp blades in a bench vise or add a little vise on top of that, but I was still very limited in work positions.
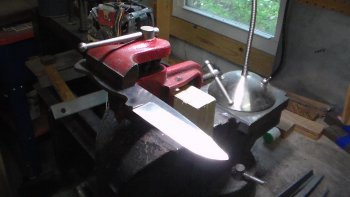
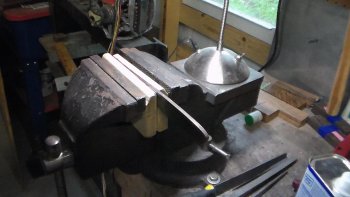
So, I started off with two pieces of stainless pipe, fairly thick walled. The tubes have about an 1/8" gap, which worked ok, but the tighter fit you get here, the better they'll clamp down without rocking.
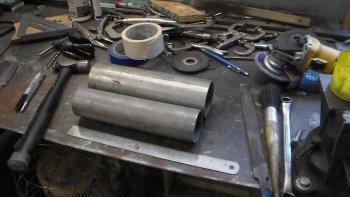
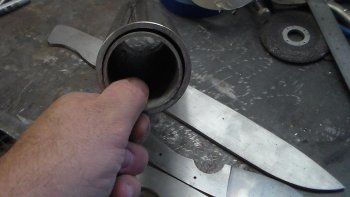
My inner tube has an i.d. of 2.125", which should handle any knife I foresee myself making. Here's a typical smaller blade and a 2" wide blade inserted.
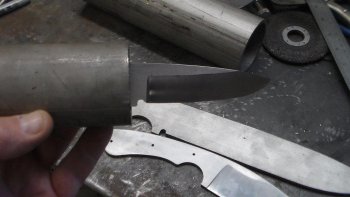
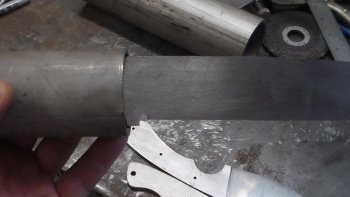
Using a piece of angle, scribe a straight line on your smaller tubing and drill and tap a hole on each end. I chose tapping my holes instead of welding nuts on the outside, in case I ever want to take it apart again.
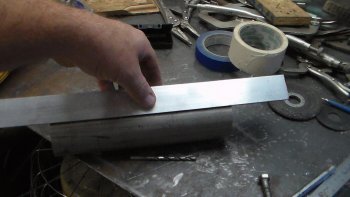
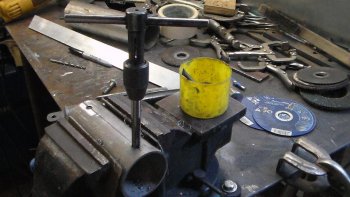
Word of caution here on your design. I'm bad about designing on the fly and made my inner tube 4.75" long and the holes are tapped very close to the ends. I wish I'd made it at least 5" wide. As you'll see later, I made some T-bolts for my clamp screws and if I spin the vise all the way over upside down, the knobs on the T-bolts sometimes interfere with the base. Not a big deal, but just a little extra length would've prevented it.
I wrestled around with how I wanted the inner vise jaws to operate. I knew the top jaw would be fixed to the T-bolts and the same length as the inner tube, but the bottom jaw(s) could be fixed, floating, short, long, etc. I decided on a floating jaw, that would be captured in the vise with notches, but could be easily lifted out and flipped end for end.
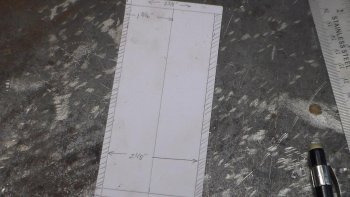
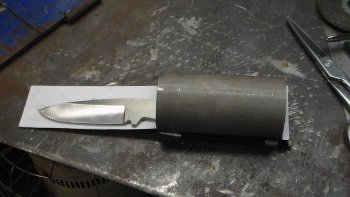
Stay tuned, more to come.......
Last edited: