So, I have cut out 6 different pocket knife patterns. Well, somewhat, in that I have the liners, and blades and springs. I have yet to cut the bolsters, but I just ran out of shop time and had to print them first anyway.
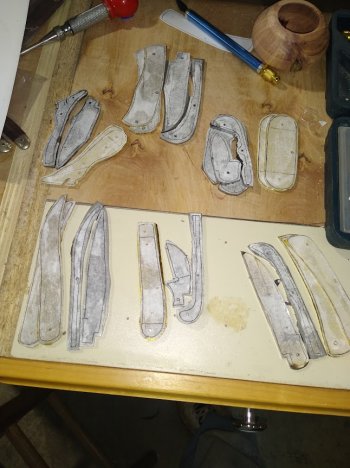
So I have also drilled them all to 1/16".
So what is the best process to grind these things "to the line"? I assume that I can pin them together with some 1/16" stock somehow or maybe superglue them one to another and do them together? Would I do the liners as a unit, or include the springs at the same time? Or is it better to do each thing one at a time, then try to get them match up later? Only one of these is a 2 blade knife (the little sunfish). If I pin them all together, do I need to peen one end of the pin or something to keep them from coming apart while grinding?
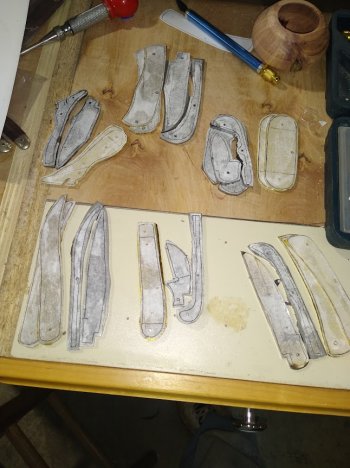
So I have also drilled them all to 1/16".
So what is the best process to grind these things "to the line"? I assume that I can pin them together with some 1/16" stock somehow or maybe superglue them one to another and do them together? Would I do the liners as a unit, or include the springs at the same time? Or is it better to do each thing one at a time, then try to get them match up later? Only one of these is a 2 blade knife (the little sunfish). If I pin them all together, do I need to peen one end of the pin or something to keep them from coming apart while grinding?