I’ve been practicing attaching bolsters to scrap of blade steel, and I’m getting pretty good and consistent results. I’m to the point where I feel like I can attach them to a blade and end up with a presentable product.
My question is this. What if anything is everyone using to attach the bolsters to the scale besides the peening of the pins? I’ve seen epoxy used, solder, nothing... I’m just curious what those with experience have used with the best results.
Thank you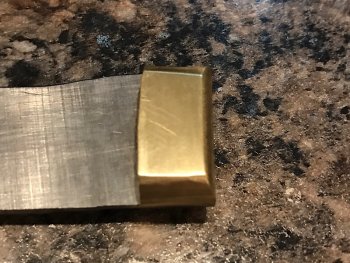
My question is this. What if anything is everyone using to attach the bolsters to the scale besides the peening of the pins? I’ve seen epoxy used, solder, nothing... I’m just curious what those with experience have used with the best results.
Thank you
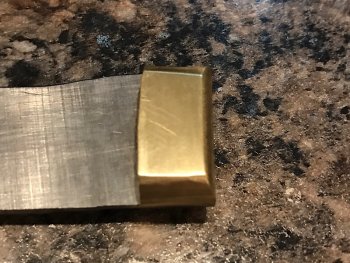