I would say that knife makers are a crafty bunch. As an expensive hobby most of us try to keep our costs down yet still want the best. Who isn't trying to get the most bang for their buck these days though? So often we shop around trying to find just that. We ask around on forums with makers whom we trust in order to get that bang. What I have also noticed though, is that it seems most people put more worth in the makers words who have been around for so long. And as well they should.....but keep in mind one thing. Usually those same folks have more of a budget then we do. I am NOT saying they are wrong (in fact I am quite sure they are correct), just that they have a bigger budget the newbie or the hobbyist and sometimes we can't afford their advice! Sure, the TW-90 machine is superb from what I've seen, but I can't afford it yet! So we need other options. I'm not a knife maker...YET. I admit, I've yet to make a single blade, I have been busy with work and also setting myself up with the right tools as I go along in order to allow myself a greater chance of success. One piece of equipment that can be pricey but I've read MOST makers believe to be indispensable is a drill press. It is an early purchase in a knife makers career and can be pricey. Benchtop models from the do it yourself stores run over $150 bucks yet I've seen first hand how horribly onstructed they are. Those of solid craftsmanship will run you $700-1200 easily.
I am not yet a knife maker, but I do know tool restoration. I have restored Vises, drill presses, band saws, jointers, antique orbital sanders and bench grinders. I believe most machines made prior to the 80's are probably better built than those of today. And they often times can be had for cheaper! I see older drill presses on Craigslist all day long (In Florida) for moderate prices and most people expect a haggle, so they can be had for a great deal....assuming you are willing to put in a little time and elbow grease! I decided to do this WIP to show that great machines can be brought back to life for cheap, and also that if a drill press is acting up (I know one recent thread was here concerning run out) you can have some advice to pull it apart and fix it.
This drill press I got off Craigslist for $65 bucks. I took it home and knew full well I was about to have an amazing drill press. It was made in 1968 and made by Rockwell (though it says Rockwell/Delta since Delta was acquired by Rockwell in the 60's), so here it is. A few shots showing the neglect and why I think some people dismiss old machines, they look different than the streamlined versions of today.
Full frontal view, doesn't look horrible, but hasn't been well maintained either.
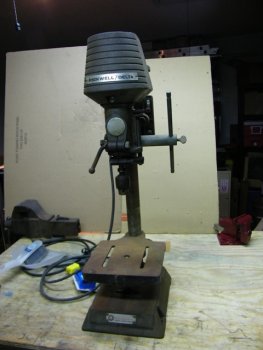
Right side view, showing the motor mount which was completely stuck. The motor belt was not tight enough and no one ever bothered to fix it, definitely could have had an issue with messing with the bearings.
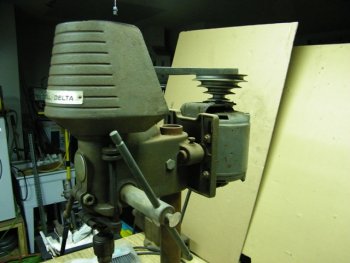
Left side view, shows more rust and minor bubbling of the paint. Turns out someone had painted this previously, ugh what a mess I discovered later!
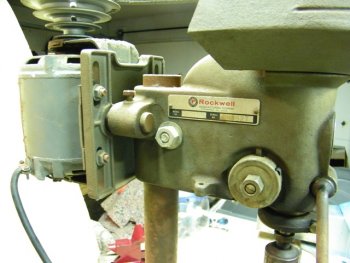
Showing the base and the table which was stuck all the way down at the base. It was stuck because the support pole had rusted up and there wasn't enough room for the table to slide up (older styles like this don't have the elevation feature).
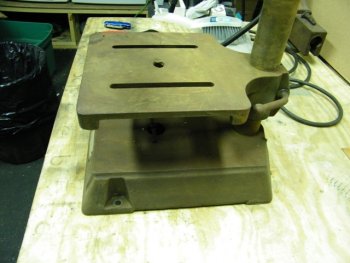
One problem I missed originally, the spindle is somehow stuck down too far below the quill.
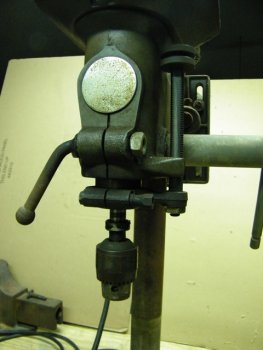
Just a simple view of the pulley cover since I wasn't sure if I would have to reproduce the label.
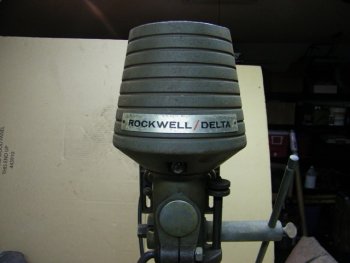
OK, Time to DIG IN! There really isn't a ton of mystery to drill presses. Depending on which year it was made certain features might not be present if its older, or added if its newer. Normally I start by raising the table up so the chuck is resting on it. Why? Because once the pinion shaft is removed (which happens early on), the quill and spindle would fall freely and WHACK right on the table or base, causing potential damage. I say normally because mine was rusted to the bottom most position. I had to use PB Blast sprayed all around the support pole so it could soak around the table. I then also used Scotch Brite pads to sand down some of the rust. Once I did that, I left it to soak overnight. The next day I came out and was able to wiggle it up to touch the base of the chuck. Took some muscle and LOTS of wiggling, but I did get it there.
First thing today, remove the tensioning spring and pinion shaft. As you can see, its just two nuts. The reason there are two is because you can't tighten the interior nut too tightly or it affects the travel of the quill and thus, the spindle (which holds the chuck). I remove one all the way, but only loosen the interior nut slightly. I only loosen the interior nut because we have to relieve the tension on the spring inside that silver cover, take it off and that cover could go flying. We remove tension by pulling the cover out slightly and turning clockwise. There are notches in the cover that align with a notch protruding from the main housing at 12 o'clock. The notch is slightly easier to see with the cover off, which can be seen in the next picture.
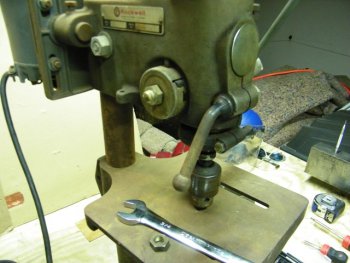
See the protruding notch at 12 and 6 o'clock? Turning it down makes it a lot less scary when done in steps!
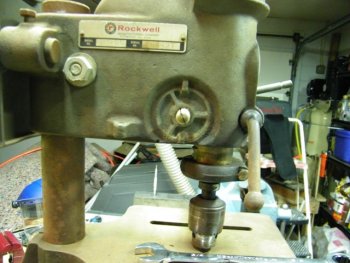
Tension spring cover, notice it has a cutout portion every 1/4 turn for adding or reducing the tension.
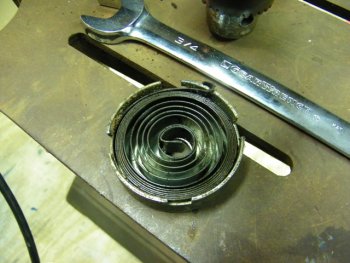
Here I've removed the depth lock assembly, since once I take out the pinion shaft, the quill can be removed but only if the depth stop has been removed first.
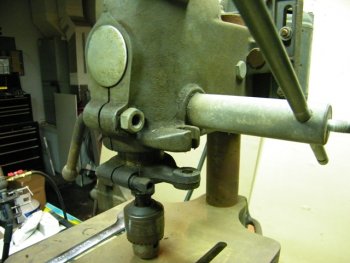
Please take note of the handle that extends to the left and angles down at a 45 degree angle, that is the quill lock. I forgot to take a picture of removing it, but basically with the table supporting the quill and spindle, the lock can be removed at anytime. It just unscrews and I set aside the washer, handle and nut for cleaning.
I think I've hit my picture limit per post, so to be continued......
I am not yet a knife maker, but I do know tool restoration. I have restored Vises, drill presses, band saws, jointers, antique orbital sanders and bench grinders. I believe most machines made prior to the 80's are probably better built than those of today. And they often times can be had for cheaper! I see older drill presses on Craigslist all day long (In Florida) for moderate prices and most people expect a haggle, so they can be had for a great deal....assuming you are willing to put in a little time and elbow grease! I decided to do this WIP to show that great machines can be brought back to life for cheap, and also that if a drill press is acting up (I know one recent thread was here concerning run out) you can have some advice to pull it apart and fix it.
This drill press I got off Craigslist for $65 bucks. I took it home and knew full well I was about to have an amazing drill press. It was made in 1968 and made by Rockwell (though it says Rockwell/Delta since Delta was acquired by Rockwell in the 60's), so here it is. A few shots showing the neglect and why I think some people dismiss old machines, they look different than the streamlined versions of today.
Full frontal view, doesn't look horrible, but hasn't been well maintained either.
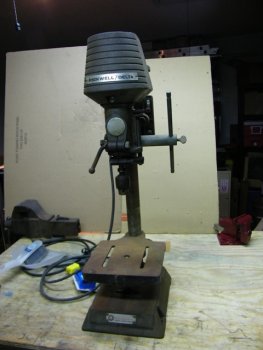
Right side view, showing the motor mount which was completely stuck. The motor belt was not tight enough and no one ever bothered to fix it, definitely could have had an issue with messing with the bearings.
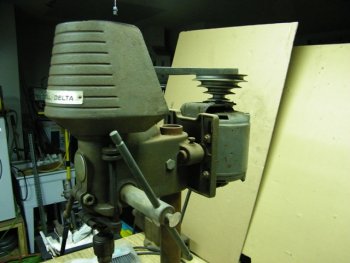
Left side view, shows more rust and minor bubbling of the paint. Turns out someone had painted this previously, ugh what a mess I discovered later!
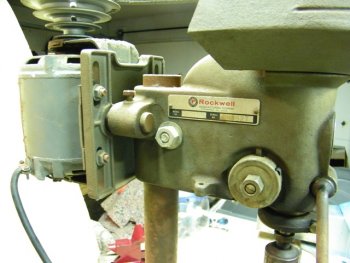
Showing the base and the table which was stuck all the way down at the base. It was stuck because the support pole had rusted up and there wasn't enough room for the table to slide up (older styles like this don't have the elevation feature).
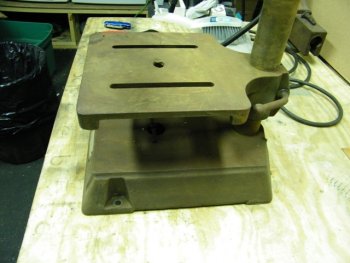
One problem I missed originally, the spindle is somehow stuck down too far below the quill.
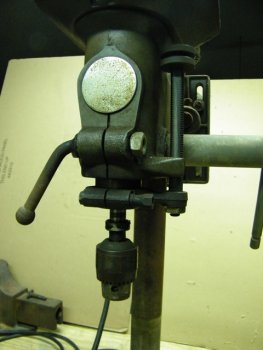
Just a simple view of the pulley cover since I wasn't sure if I would have to reproduce the label.
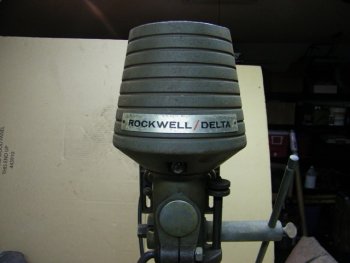
OK, Time to DIG IN! There really isn't a ton of mystery to drill presses. Depending on which year it was made certain features might not be present if its older, or added if its newer. Normally I start by raising the table up so the chuck is resting on it. Why? Because once the pinion shaft is removed (which happens early on), the quill and spindle would fall freely and WHACK right on the table or base, causing potential damage. I say normally because mine was rusted to the bottom most position. I had to use PB Blast sprayed all around the support pole so it could soak around the table. I then also used Scotch Brite pads to sand down some of the rust. Once I did that, I left it to soak overnight. The next day I came out and was able to wiggle it up to touch the base of the chuck. Took some muscle and LOTS of wiggling, but I did get it there.
First thing today, remove the tensioning spring and pinion shaft. As you can see, its just two nuts. The reason there are two is because you can't tighten the interior nut too tightly or it affects the travel of the quill and thus, the spindle (which holds the chuck). I remove one all the way, but only loosen the interior nut slightly. I only loosen the interior nut because we have to relieve the tension on the spring inside that silver cover, take it off and that cover could go flying. We remove tension by pulling the cover out slightly and turning clockwise. There are notches in the cover that align with a notch protruding from the main housing at 12 o'clock. The notch is slightly easier to see with the cover off, which can be seen in the next picture.
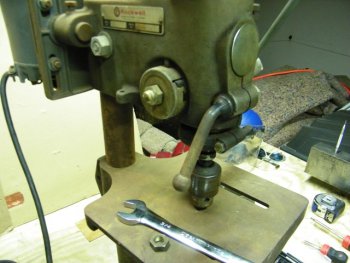
See the protruding notch at 12 and 6 o'clock? Turning it down makes it a lot less scary when done in steps!
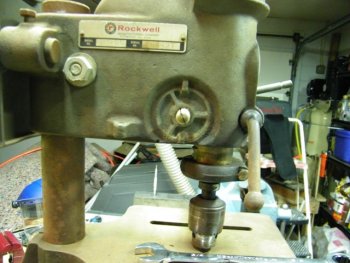
Tension spring cover, notice it has a cutout portion every 1/4 turn for adding or reducing the tension.
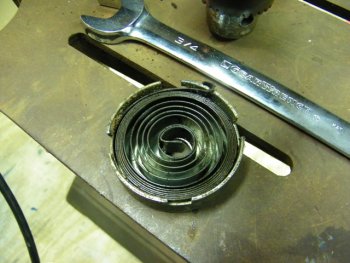
Here I've removed the depth lock assembly, since once I take out the pinion shaft, the quill can be removed but only if the depth stop has been removed first.
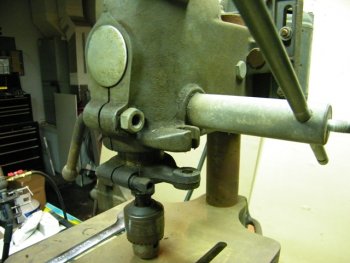
Please take note of the handle that extends to the left and angles down at a 45 degree angle, that is the quill lock. I forgot to take a picture of removing it, but basically with the table supporting the quill and spindle, the lock can be removed at anytime. It just unscrews and I set aside the washer, handle and nut for cleaning.
I think I've hit my picture limit per post, so to be continued......
Last edited: