Hey everyone, new to the forum and so glad I found it. I have been a reseller for a while now, but am starting to design and sell my own brand of knives. As background, I have my knife designs already done and its pretty sweet to see them carved on the CNC machine, I do all my design in Fusion 360 and so far all my knives are fixed blade knives. I have been using a simple Softjaw for the flip side but unfortunately I am running into serious chatter when I am carving the the longer knives because it isn't fully supported on backside and the machine is leaving serious gouges in my blades, which are clearly visible in the attached picture of two knives i ran yesterday.
I'm curious to learn how you all do your knife workholding/pallets to make sure your blades are fully supported while using an 3D Adaptive Tool path?? I cant figure out how to hold them down to carve the second side and still use a 3D adaptive toolpath to hog all the metal out around the top and sides and start the contour on the blade. I might need to change my Tool Paths but would love to hear your feedback on this subject.
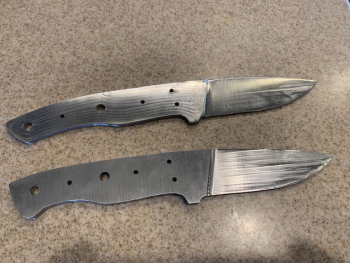
I'm curious to learn how you all do your knife workholding/pallets to make sure your blades are fully supported while using an 3D Adaptive Tool path?? I cant figure out how to hold them down to carve the second side and still use a 3D adaptive toolpath to hog all the metal out around the top and sides and start the contour on the blade. I might need to change my Tool Paths but would love to hear your feedback on this subject.
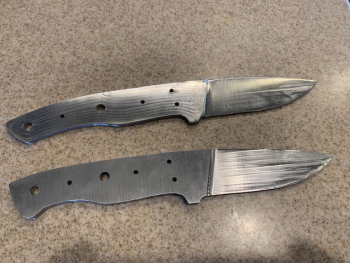