Time to finish up this knife. Here are the final pics of this build. Hope you enjoy.
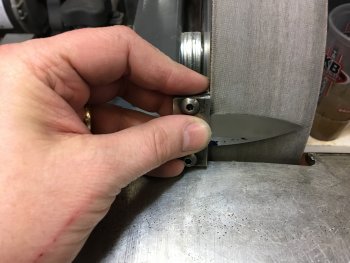
If you recall, we left off last week with marking the grind lines on the blade and fastening the blade in my file guide. Here I am hollow grinding the bevels on the blade. I freehand my grinds, but I do like to have my tool rest in place to give my hands a little support.
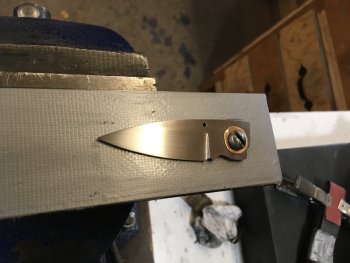
After grinding in the bevels on the blade, it's time to do some hand sanding. I finish my blades up to 600 grit.
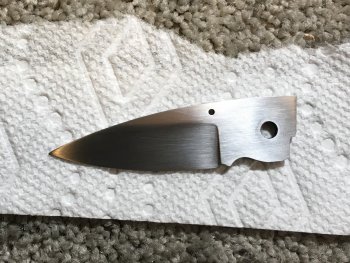
The blade is all finished with a nice 600 grit satin.
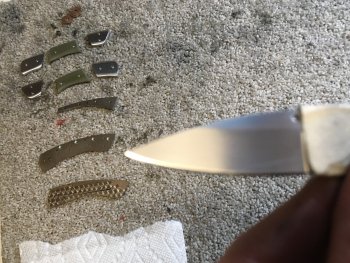
I like to put the edge on my blades before I assemble them. There is less of a chance of messing up if I do it this way. I wrap a piece of tape around the ricasso and tang to protect those areas.
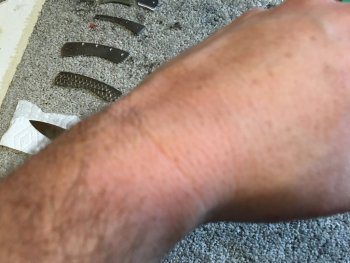
The obligatory arm hair shave. It's sharp!
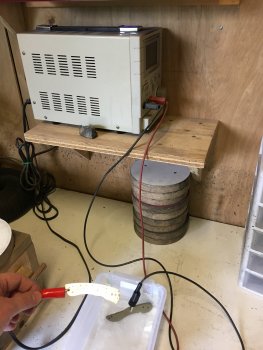
Here is my anodizing setup. It consists of an electrolyte bath (water and borax), a DC power source, and a pair of leads. The negative lead gets attached to an old piece of O1 steel, which is actually a failed liner from my first folding knife ever, and placed in the bath. The positive lead gets attached to the liner that will be anodized.

And here are the liners after being anozided a deep bronze color. Nice!
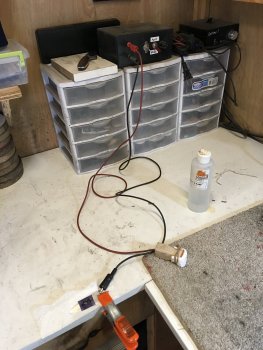
Here is my setup for putting my maker's mark on the blade. I use a power source that I build from online plans. With my maker's mark stencil taped to the blade, I use my setup to etch the mark into the blade.
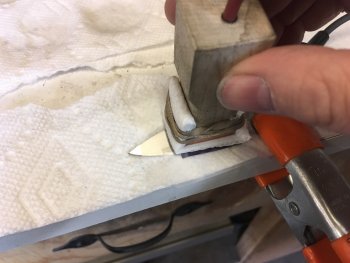
Here I am etching the mark on the blade. I use a piece of folded up paper towel for my etching pad. I've found it works as well as the commercially available pads but cost much less.