J S Machine
Well-Known Member
I started using bearings in my folders a few years ago, and I really like the smooth performance. However, a problem I have fought with constantly is the blade gap between the blade itself and the handle sides.
I use some bearings which are some of the smallest available. They have a .125" hole in the carrier and the balls themselves are .0625". My problem is that I cannot figure out what the best way is to recess and get the gap between the blade and handles on each side I want.
Here is an example of three options that I have tried.
In these examples, the blade is green, pivot is red, liners are yellow, bolsters are light blue, and the bearings are pink.
The first option (Option A) is what I encountered the first time I assembled one without any recesses. I essentially had a 1/16" gap on either side of the blade. This just looked way too big to me, so I started to work on getting some recesses in to help close the gap. Once I went as far as I could go on the liners (Option B) where I still felt comfortable with the amount of material there, it still wasn't enough. My liners were thin on that particular knife so there wasn't much to work with.
Since I had no other option at that point, I moved to the blade and recessed it (Option C). A major pain too..because I had to use carbide since it was already hard. I ended up with a combination of both Option B and C to close the gap.
I was just wondering how you guys close this gap?
I'm fixing to do another couple of folders with bearings, and I want to review all the possible options first.
I like the idea of option B above, but the way I am thinking, the liners will be completely cut out and the bearing will actually ride on the bolster surface. I'm not sure how to make this work other than to be absolutely sure that the bolsters are securely attached to the liners..maybe with screws from the backside of the liners so they are not seen?
Just a big headache. I like bearings, but I don't like how it makes me do a bunch of extra work to make the knife clearances look right.
On a related note - How about the long term affects of those ball bearings on Ti? Will it eventually wear a groove and compromise the pivot? What about damascus blades? Do you ever allow a ball bearing to roll on the surface of Damascus? I would think the blade would produce a gritty feeling when opened and closed, because of the alternating metal types and hardness of each.
Maybe Teflon or bronze friction washers are not so bad after all. Lol
I use some bearings which are some of the smallest available. They have a .125" hole in the carrier and the balls themselves are .0625". My problem is that I cannot figure out what the best way is to recess and get the gap between the blade and handles on each side I want.
Here is an example of three options that I have tried.
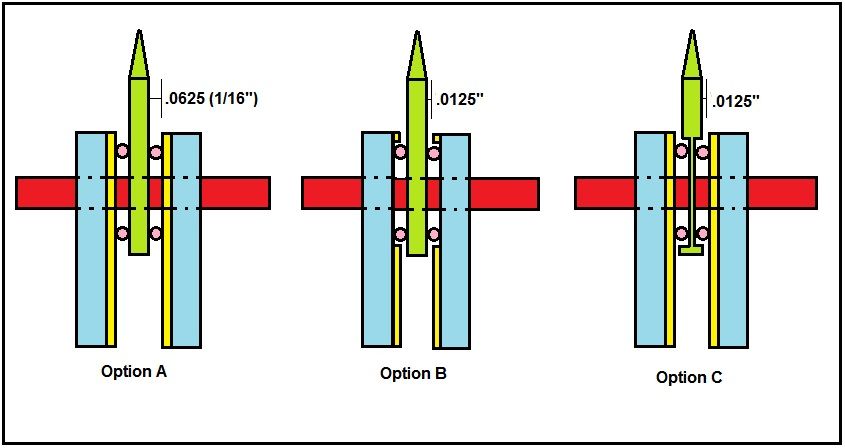
In these examples, the blade is green, pivot is red, liners are yellow, bolsters are light blue, and the bearings are pink.
The first option (Option A) is what I encountered the first time I assembled one without any recesses. I essentially had a 1/16" gap on either side of the blade. This just looked way too big to me, so I started to work on getting some recesses in to help close the gap. Once I went as far as I could go on the liners (Option B) where I still felt comfortable with the amount of material there, it still wasn't enough. My liners were thin on that particular knife so there wasn't much to work with.
Since I had no other option at that point, I moved to the blade and recessed it (Option C). A major pain too..because I had to use carbide since it was already hard. I ended up with a combination of both Option B and C to close the gap.
I was just wondering how you guys close this gap?
I'm fixing to do another couple of folders with bearings, and I want to review all the possible options first.
I like the idea of option B above, but the way I am thinking, the liners will be completely cut out and the bearing will actually ride on the bolster surface. I'm not sure how to make this work other than to be absolutely sure that the bolsters are securely attached to the liners..maybe with screws from the backside of the liners so they are not seen?
Just a big headache. I like bearings, but I don't like how it makes me do a bunch of extra work to make the knife clearances look right.
On a related note - How about the long term affects of those ball bearings on Ti? Will it eventually wear a groove and compromise the pivot? What about damascus blades? Do you ever allow a ball bearing to roll on the surface of Damascus? I would think the blade would produce a gritty feeling when opened and closed, because of the alternating metal types and hardness of each.
Maybe Teflon or bronze friction washers are not so bad after all. Lol