"Wedding Knife in Purpleheart"
CPM-S35VN partial tang construction
Purpleheart handle
Titanium guard
7 3/4" edge length .05" thick
13" OAL
Single sided bevel at 15°
RHC 60
CLICK FOR LARGER IMAGE
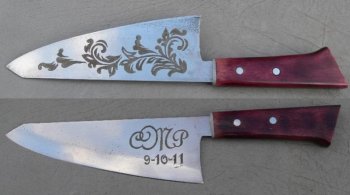
This is a wedding cake knife for my Sister-in-law's wedding last weekend. She wanted a knife to cut the cake and serve it with. I've wanted to make this knife almost since I started making knives last year. I will be making this knife again while correcting the flaws.
First, what I like about this knife.
1. The blade shape and geometry turned out exactly as I envisioned.
2. CPM-S35VN Let's see how this stuff holds an edge. Thanks to TAIT for sending me the metal to use.
3. Whole blade bath electro-etching. While I'm certain that I'll learn more tips & tricks to this, it turned out pretty nice with the monogram on one side and decorative on the other.
4. The handle! I love the purpleheart and how it turned out. It was the first time I used purpleheart as well as my first partial tang. The uneven coloring looks magnificent.
5. Sharp! Very sharp. The best job sharpening I've done yet.
6. Chisel ground. My very first chisel ground knife. I didn't do this because it's easier, it's not, but because that's the way many Japanese knives are.
This knife had four major failures.
1. A bit of deep decarb right beneath the monogram. I blame the steel for this, there was nothing wrong with the foil it was wrapped in and the blade was clean. There is a huge decarb on the tang, luckily it's on the tang and not the blade. It's so bad, I would have had to scrap the knife had it been on the blade.
2. Surface grinding failed. Should have surface ground it before grinding the bevel. Surfacing after the bevel left a mass of mill scale at the bottom point by the etching where the grinding wheel was on the back side of the bevel.
3. Etching failure. When I etched the whole knife in a bath, the paint failed and little spots etched all over the knife. This happened because I used my anodizing bath lead which is titanium. Had I used a steel lead instead, it would have been better.
4. Purpleheart. I milled out the partial tang slot and glued the two halves together. After I had the handle all sanded and drilled pretty looking, I scorched it to bring out the purple. The purple came out but the wood warped and cracked the glue around the tang(only 1/8" wide on the top and bottom of the tang). Good thing I decided to use corby bolts for decoration. The handle would have been useless if I hadn't.
Small flaws
The bevel isn't even at the point by the monogram
The edge isn't even at the point by the monogram
A bit of decarb during the HT required me to resand the blade post-HT. I'm probably going to send any stainless out for HT in the future. Too much hassle trying to hand sand all that vanadium after it's been hardened.
With a different wood, I could have done a better job on the handle. Purpleheart is a tan/red wood. When you scorch it with a heat gun or torch it turns purple. If you sand the purple the tan/red shows. If I sand through the CA finish it sands off the purple. Trying to scorch the wood ruins the surrounding CA. Therefore, I had to be overly gentle with the sanding and couldn't get it as smooth as I wanted.
I should have scrapped the knife after the decarb during HT because it's too deep to grind out and keep the knife's shape. The same with the mill scale on the back side of the bevel. I finished the knife because it's the only piece of S35VN that's I have this size and didn't have enough time to start over. It's good to get the experience from finishing the knife, even if the knife is a failure. If I hadn't finished the knife, I wouldn't have learned from the mistakes made in the purpleheart and etching. I didn't mark this knife because it's a practice knife at this point. It will still get used in the wedding. In the lighting at the reception, no one will notice. I'll start working on her replacement next week.
--
CPM-S35VN partial tang construction
Purpleheart handle
Titanium guard
7 3/4" edge length .05" thick
13" OAL
Single sided bevel at 15°
RHC 60
CLICK FOR LARGER IMAGE
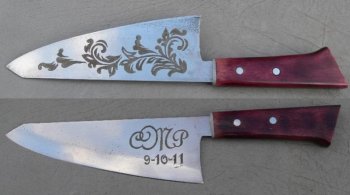
This is a wedding cake knife for my Sister-in-law's wedding last weekend. She wanted a knife to cut the cake and serve it with. I've wanted to make this knife almost since I started making knives last year. I will be making this knife again while correcting the flaws.
First, what I like about this knife.
1. The blade shape and geometry turned out exactly as I envisioned.
2. CPM-S35VN Let's see how this stuff holds an edge. Thanks to TAIT for sending me the metal to use.
3. Whole blade bath electro-etching. While I'm certain that I'll learn more tips & tricks to this, it turned out pretty nice with the monogram on one side and decorative on the other.
4. The handle! I love the purpleheart and how it turned out. It was the first time I used purpleheart as well as my first partial tang. The uneven coloring looks magnificent.
5. Sharp! Very sharp. The best job sharpening I've done yet.
6. Chisel ground. My very first chisel ground knife. I didn't do this because it's easier, it's not, but because that's the way many Japanese knives are.
This knife had four major failures.
1. A bit of deep decarb right beneath the monogram. I blame the steel for this, there was nothing wrong with the foil it was wrapped in and the blade was clean. There is a huge decarb on the tang, luckily it's on the tang and not the blade. It's so bad, I would have had to scrap the knife had it been on the blade.
2. Surface grinding failed. Should have surface ground it before grinding the bevel. Surfacing after the bevel left a mass of mill scale at the bottom point by the etching where the grinding wheel was on the back side of the bevel.
3. Etching failure. When I etched the whole knife in a bath, the paint failed and little spots etched all over the knife. This happened because I used my anodizing bath lead which is titanium. Had I used a steel lead instead, it would have been better.
4. Purpleheart. I milled out the partial tang slot and glued the two halves together. After I had the handle all sanded and drilled pretty looking, I scorched it to bring out the purple. The purple came out but the wood warped and cracked the glue around the tang(only 1/8" wide on the top and bottom of the tang). Good thing I decided to use corby bolts for decoration. The handle would have been useless if I hadn't.
Small flaws
The bevel isn't even at the point by the monogram
The edge isn't even at the point by the monogram
A bit of decarb during the HT required me to resand the blade post-HT. I'm probably going to send any stainless out for HT in the future. Too much hassle trying to hand sand all that vanadium after it's been hardened.
With a different wood, I could have done a better job on the handle. Purpleheart is a tan/red wood. When you scorch it with a heat gun or torch it turns purple. If you sand the purple the tan/red shows. If I sand through the CA finish it sands off the purple. Trying to scorch the wood ruins the surrounding CA. Therefore, I had to be overly gentle with the sanding and couldn't get it as smooth as I wanted.
I should have scrapped the knife after the decarb during HT because it's too deep to grind out and keep the knife's shape. The same with the mill scale on the back side of the bevel. I finished the knife because it's the only piece of S35VN that's I have this size and didn't have enough time to start over. It's good to get the experience from finishing the knife, even if the knife is a failure. If I hadn't finished the knife, I wouldn't have learned from the mistakes made in the purpleheart and etching. I didn't mark this knife because it's a practice knife at this point. It will still get used in the wedding. In the lighting at the reception, no one will notice. I'll start working on her replacement next week.
--