OK REMIST17, I'm gonna take you where no man has gone before. Welcome to my shop in Las Cruces, New Mexico.
View attachment 51917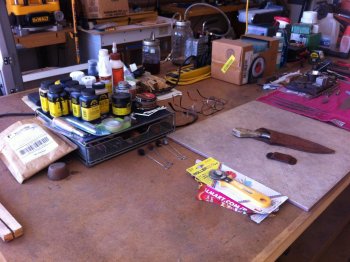
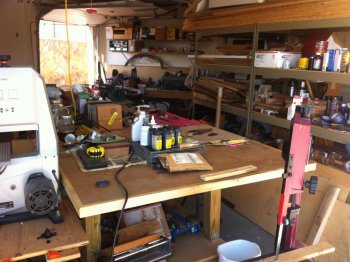
I have been making knives for about a year now and I am still using a HF 1 X 30 grinder although I just ordered an LB 1000 yesterday. Initially I had the same problem you have and it took a bunch of trial and error to figure out the solution that worked for me. As you can see, the view from my shop is beautiful and I spent a lot of time gazing out at the mountains in an effort to keep from killing myself after screwing up another piece of steel on my 1 X 30. Eventually, I came up with the Rube Goldberg of all Rube Goldberg solutions so here it is:
This is my 1 X 30) with all its mods. First I extended the platen upward by about 2" to accommodate the larger kitchen knives I make and then I extended the work table by adding a 6" X 24" X 1/4" aluminum plate to the top of the existing table.
I always check level and square before I grind anything.
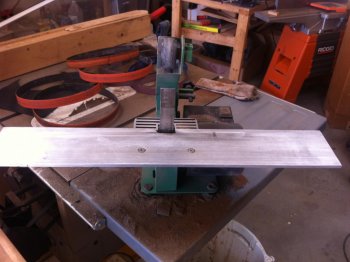
Next I cut about 4 2 X 4s about 16" long and went to my planer. I flattened every 2X4 perfectly flat. Then on one edge of 1 2X4 I planed it to 1* out of square (or 44*) then I marked that edge 1* with a sharpie. Then on the other edge of that same 2X4 I planed it to 2* out of square (or 43*) and marked it 2*. Next I took another perfectly flat 16" long 2X4 and planed one edge to 5* out of square (or 40*) and marked it 5*. On the other edge I made it 10*. On the third 2X4 I set one edge to 20* on one edge and O*. As you might notice, these are the basic degrees that you generally need to grind a flat grind to.
The boards look like this.
Now, once my knife is cut out and profiled I drill my pin holes and weight reduction holes in the handle. Then, depending on the thickness of the blade and the height of the blade I select one edge of my prepared 2X4s and using the pin hole I screw the knife blade, cutting edge up, to the 2X4 edge I need i.e. 2*. Say it's a 1.5" tall by 5/32 thick blade I will select the 2* edge and attach the blade to it. When I then lay the flat edge of the 2X4 on my work table it presents the blade to the belt at a 2* slant which I know from experience will allow me to remove material from the blade edge moving to the middle and up the blade to the top and I will arrive at both places at about the same time.
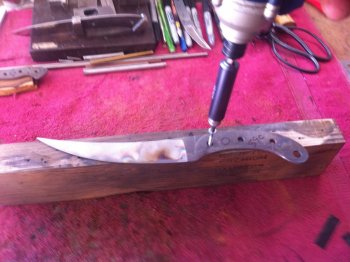
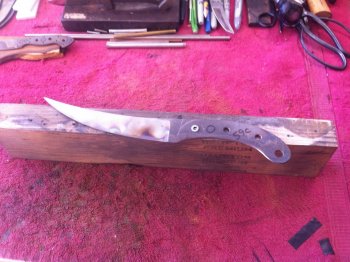
You notice I said "about" the same time - for a bunch of reasons the system isn't quite as perfect as it needs to be so here is the final piece of the puzzle. As I am grinding I may notice that I am getting closer to the top of the blade faster than I am approaching my center scribe line on the edge of the blade so I need to adjust my angle just slightly to correct that. The correction is to tilt the edge of the blade just slightly toward the belt so what I do is, using masking tape, I run several thicknesses of masking tape along the bottom flat portion of the 2X4 that is farthest from the belt. That serves to just slightly tip the knife edge just slightly closer to the belt and the top edge of the blade just slightly farther away from the belt. (See my really bad diagram).
As you can see, I have accumulated a lot of these masking tape shim over time and they each have a purposes As I have worked this system I have learned to fine tune the process where I can now grind flat grinds to 1300 grit and move directly to my buffer to mirror finish. It was a long, slow process to get to this point but it works for me. Hope this helps you slay some demons.
Wallace