Josh Dabney
Moderator
Ok fellas here's what I got.
I finally got some Parks 50 quench oil so I forged out this 4" hunter blade over the weekend as a test blade for my HT and developing hamon.
Here are the specifics.
-Steel- 1095 from Aldo
-Rough forged at 2000 degrees
-Refined forging at 1800
-Normalized at 1600, 1500, and twice at 1450
-Rough ground to .050 on the edge
-Sub critical anneal 1 hour at 1300 drop 50 degrees an hour to 900 cool the rest of the way in the oven
-Follow Stephen Fowlers tutorial for clay using a skim coat over the entire blade and making the clay on the ricasso, spine, and lines approx 1/8" thick and matching on both sides
-Into a 1425 degree oven, wait for temp to come back up then soak 20 minutes
-Quench in Parks 50 pre-heated to 100 degrees for approx 10 seconds. Blade still hot enough to throw smoke at this point
-Scrape off clay, file check, then into the oven at 400 for 2 hours.
This isn't a super clean finish but I wanted to get it clean enough to get a clear look at whats going on so It's hand sanded to 1000 on all but the tip and plunge (with the exeption of some verticle scratches)
This pic shows the blade as it's fresh out of the ferric and still wet and untouched. I was trying to catch what I could see with my eye in the pic and any clean-up out of the etch made the detail in the upper portion of the blade invisible.
The white cloudy looking area shows right where the clay was applied. I was worried with the speed of the parks that it would harden underneath the clay but that was definately not a problem.
Any help or suggestions as to which variable to change would be greatly appreciated !
Thanks alot fellas, Josh
I finally got some Parks 50 quench oil so I forged out this 4" hunter blade over the weekend as a test blade for my HT and developing hamon.
Here are the specifics.
-Steel- 1095 from Aldo
-Rough forged at 2000 degrees
-Refined forging at 1800
-Normalized at 1600, 1500, and twice at 1450
-Rough ground to .050 on the edge
-Sub critical anneal 1 hour at 1300 drop 50 degrees an hour to 900 cool the rest of the way in the oven
-Follow Stephen Fowlers tutorial for clay using a skim coat over the entire blade and making the clay on the ricasso, spine, and lines approx 1/8" thick and matching on both sides
-Into a 1425 degree oven, wait for temp to come back up then soak 20 minutes
-Quench in Parks 50 pre-heated to 100 degrees for approx 10 seconds. Blade still hot enough to throw smoke at this point
-Scrape off clay, file check, then into the oven at 400 for 2 hours.
This isn't a super clean finish but I wanted to get it clean enough to get a clear look at whats going on so It's hand sanded to 1000 on all but the tip and plunge (with the exeption of some verticle scratches)
This pic shows the blade as it's fresh out of the ferric and still wet and untouched. I was trying to catch what I could see with my eye in the pic and any clean-up out of the etch made the detail in the upper portion of the blade invisible.
The white cloudy looking area shows right where the clay was applied. I was worried with the speed of the parks that it would harden underneath the clay but that was definately not a problem.
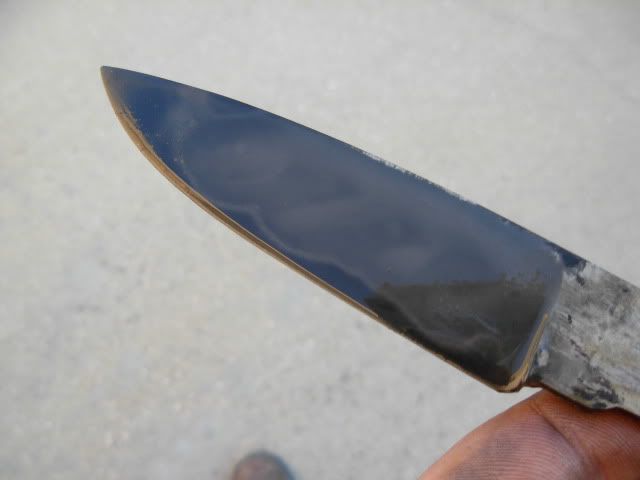
Any help or suggestions as to which variable to change would be greatly appreciated !
Thanks alot fellas, Josh