RickA
Well-Known Member
Hey Everyone
A belated Happy New Year to you all, hope 2014 is an awesome year for everyone on the forum.
After my success with my club competition Bowie (http://knifedogs.com/showthread.php?34604-Club-Competition-Bowie) my colleagues asked me if I would make a hunting knife for our boss, who was made redundant due to a company restructuring exercise. I said I would be happy to, and started some planning (beginning with a bit of research on the forums).
After my previous thread on advice for a hunting knife I spent some time drawing up some ideas. I decided to cut and grind 2 of my own design and 2 based on a Loveless Dropped hunter template I found online (which turned out to be a bit inaccurate - the blade is 1/3" too short and the tang shape is slightly wrong). I cut out four blanks (all Bohler N690) - 2x 3.2mm and 2x 5mm, I profile ground the blanks before hollow grinding, added some filework to the back of the blade and then took them in for hardening.
I decided to make the knife for my boss based on my own design, using the 5mm N690 blank and adding 316 stainless bolsters and Desert Ironwood scales with thin red formica liners. I order some Desert Ironwood from a local supplier but due to the time of year and the shop moving premises I only received it after Christmas. I finally knuckled down on Boxing day and started getting it together.
I finished it last weekend. You will see that the bolsters are partially "stippled" - this was a "rescue job". Initially my bolsters were to be mirror polished, I profiled, shaped and mirror polished the front faces of the bolsters, however after peening the pins and grinding the bolsters (everything looked good) until I proceeded to start shaping the bottom of the bolsters - at which point half of one one of the pins became visible (just less than half the circumference) - either it wasn't peened properly or the pin material had a dent / scratch). Unfortunately the pin was on the curved area at the bottom of the bolster - so drilling it out and redoing it would have been a problem - so I ended up masking off the bolster, and stippling it with a 3mm Tungsten carbide ball burr in a Dremel - followed by a brass brush wheel and then a light buffing to smooth and shine the low areas of the stippling - before finishing off with 800# water paper hand rubbed). The front faces of the bolsters are still mirrored.
One thing I did this time and will certainly do in future, which I haven't done before was to create a hardwood blank of the handle/bolster area and shape it into the desired handle shape first - before I started shaping the actual handle, to ensure I got a very comfortable fit and no sharp / hard edges to cause pain / discomfort with use.
I took the knife up country on Wednesday to present it to him, unfortunately he wasn't there the past couple of days so my colleagues said that they would hand it to him today, after I had returned home. I'm waiting to hear what he thought of it.
The last photo is of the knife in the presentation wood box I delivered it in. I'm not sure how viable it is to do this with every knife (unless I take up box making myself), but it is definitely a very nice way to present the knife as a gift. I have a friend who uses similar boxes with his makers logo laser engraved on the box lid. I did manage to have a stamp made of my makers logo for my sheaths, which you can see on the picture of the back of the sheath.
Please let me know what you think? The details are as follows
10cm / 4" fileworked hollowground blade of 5mm N690 @ 60Rc
316 Stainless bolsters, pins and lanyard tube
Arizona Desert Ironwood scales with red formica liners
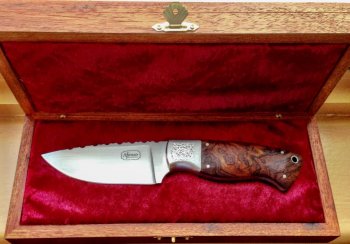
A belated Happy New Year to you all, hope 2014 is an awesome year for everyone on the forum.
After my success with my club competition Bowie (http://knifedogs.com/showthread.php?34604-Club-Competition-Bowie) my colleagues asked me if I would make a hunting knife for our boss, who was made redundant due to a company restructuring exercise. I said I would be happy to, and started some planning (beginning with a bit of research on the forums).
After my previous thread on advice for a hunting knife I spent some time drawing up some ideas. I decided to cut and grind 2 of my own design and 2 based on a Loveless Dropped hunter template I found online (which turned out to be a bit inaccurate - the blade is 1/3" too short and the tang shape is slightly wrong). I cut out four blanks (all Bohler N690) - 2x 3.2mm and 2x 5mm, I profile ground the blanks before hollow grinding, added some filework to the back of the blade and then took them in for hardening.
I decided to make the knife for my boss based on my own design, using the 5mm N690 blank and adding 316 stainless bolsters and Desert Ironwood scales with thin red formica liners. I order some Desert Ironwood from a local supplier but due to the time of year and the shop moving premises I only received it after Christmas. I finally knuckled down on Boxing day and started getting it together.
I finished it last weekend. You will see that the bolsters are partially "stippled" - this was a "rescue job". Initially my bolsters were to be mirror polished, I profiled, shaped and mirror polished the front faces of the bolsters, however after peening the pins and grinding the bolsters (everything looked good) until I proceeded to start shaping the bottom of the bolsters - at which point half of one one of the pins became visible (just less than half the circumference) - either it wasn't peened properly or the pin material had a dent / scratch). Unfortunately the pin was on the curved area at the bottom of the bolster - so drilling it out and redoing it would have been a problem - so I ended up masking off the bolster, and stippling it with a 3mm Tungsten carbide ball burr in a Dremel - followed by a brass brush wheel and then a light buffing to smooth and shine the low areas of the stippling - before finishing off with 800# water paper hand rubbed). The front faces of the bolsters are still mirrored.
One thing I did this time and will certainly do in future, which I haven't done before was to create a hardwood blank of the handle/bolster area and shape it into the desired handle shape first - before I started shaping the actual handle, to ensure I got a very comfortable fit and no sharp / hard edges to cause pain / discomfort with use.
I took the knife up country on Wednesday to present it to him, unfortunately he wasn't there the past couple of days so my colleagues said that they would hand it to him today, after I had returned home. I'm waiting to hear what he thought of it.
The last photo is of the knife in the presentation wood box I delivered it in. I'm not sure how viable it is to do this with every knife (unless I take up box making myself), but it is definitely a very nice way to present the knife as a gift. I have a friend who uses similar boxes with his makers logo laser engraved on the box lid. I did manage to have a stamp made of my makers logo for my sheaths, which you can see on the picture of the back of the sheath.
Please let me know what you think? The details are as follows
10cm / 4" fileworked hollowground blade of 5mm N690 @ 60Rc
316 Stainless bolsters, pins and lanyard tube
Arizona Desert Ironwood scales with red formica liners
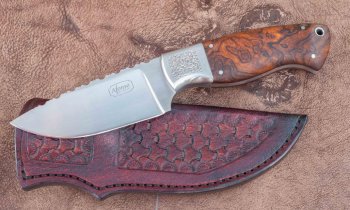
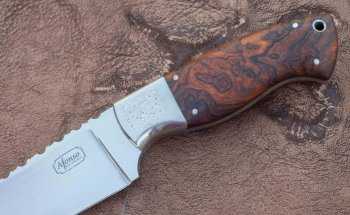
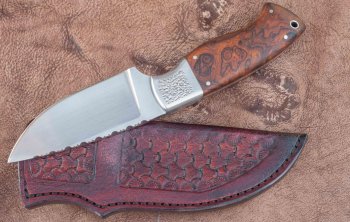
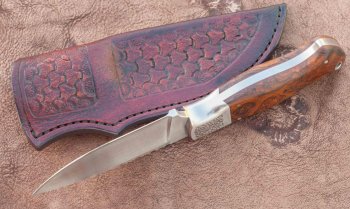
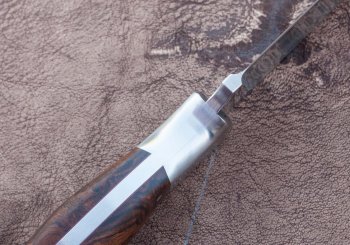
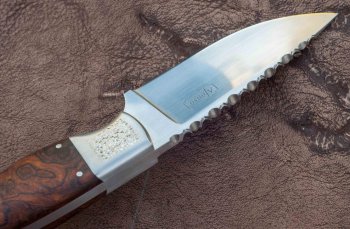
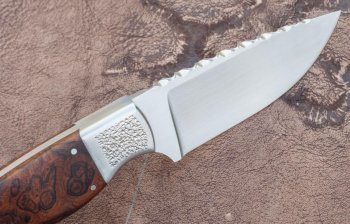
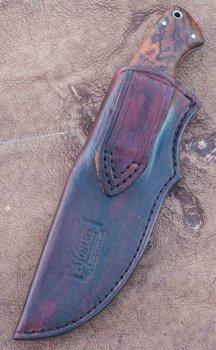
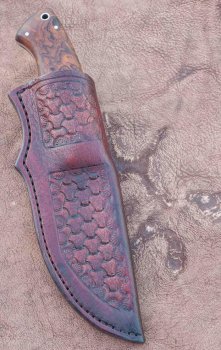
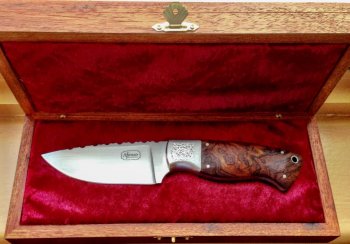
Last edited: