Mike Fennessy
Member
Here's how I make my leather sheaths. Some of it might look familiar if you've seen Chuck Burrows excellent DVD. I've also learned a lot from Paul Long's and John Bianchi's DVDs.
I didn't make this knife, someone wanted me reprofile the blade and then decided they wanted me to make a sheath for it also.
Layout:
First I lay the blade, spine down and centered on a manila folder. Then, roll it over to one side. This will take the thickness of the handle into account.
(edit: changed 5/16" to 1/2" in the following paragraphs, the 5/16" is for a much smaller model)
I measure over about 1/2" all the way around the blade side. Also around the tip if you're going to sew around the tip, which I always do. It’s a small touch that I think sets it apart and doesn’t add much work at all. You don't have to make it quite so wide on the back side of the tip since there wont be a welt there.
When you get to the widest point of the knife, usually the guard or near the ricasso, you can stop outlining the knife and just make the shape whatever design you want from their up, as long as it's 1/2" wider than the widest part. In the picture you can see I went wider than 1/2" at the widest point so that I could put a slight curve on the top third of the sheath.
By the way, 1/2" is a little wider than you need but I would rather adjust later and have more material to take off than have to scrap it because I ran out of room, which used to happen to me quite a bit.
The top you can shape however you want, just make sure that it will be an even swoop across the top when you cut out the pattern or you might have a hard time sanding it later. I make sure the center curve fits the smallest wheel I have (2")
Draw a line from the widest point straight up to the top of the sheath. This will be the pattern for the welt. Here I've drawn that in in blue so you can see it better. Don't cut it out yet, we'll do that after transferring the bigger pattern to the leather.
If you have to bring two cuts together in a 'V', put a small hole that you can cut out from so the leather doesn't split later.
I didn't make this knife, someone wanted me reprofile the blade and then decided they wanted me to make a sheath for it also.
Layout:
First I lay the blade, spine down and centered on a manila folder. Then, roll it over to one side. This will take the thickness of the handle into account.
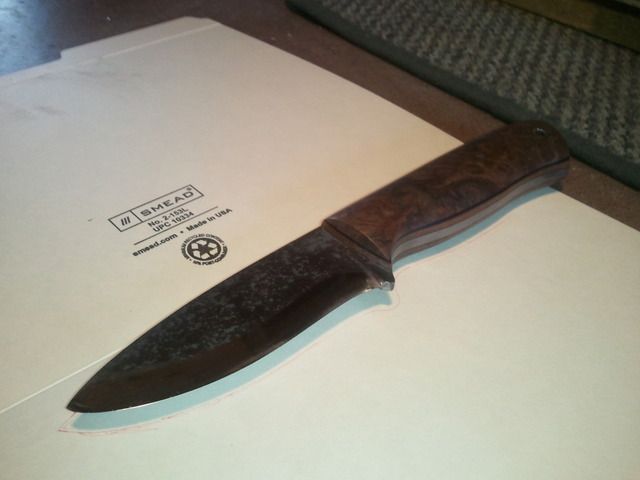
(edit: changed 5/16" to 1/2" in the following paragraphs, the 5/16" is for a much smaller model)
I measure over about 1/2" all the way around the blade side. Also around the tip if you're going to sew around the tip, which I always do. It’s a small touch that I think sets it apart and doesn’t add much work at all. You don't have to make it quite so wide on the back side of the tip since there wont be a welt there.
When you get to the widest point of the knife, usually the guard or near the ricasso, you can stop outlining the knife and just make the shape whatever design you want from their up, as long as it's 1/2" wider than the widest part. In the picture you can see I went wider than 1/2" at the widest point so that I could put a slight curve on the top third of the sheath.
By the way, 1/2" is a little wider than you need but I would rather adjust later and have more material to take off than have to scrap it because I ran out of room, which used to happen to me quite a bit.
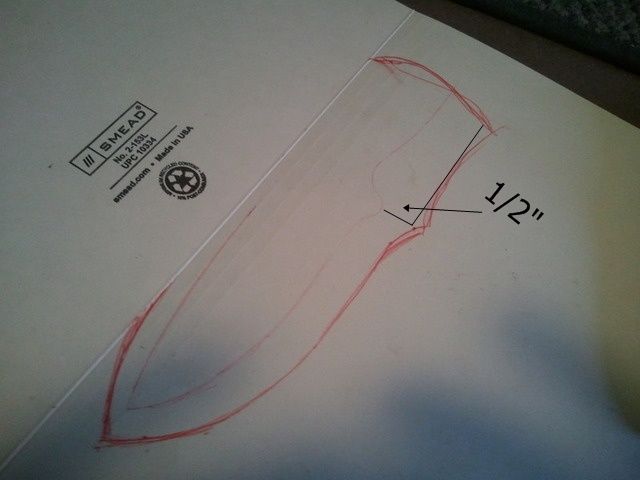
The top you can shape however you want, just make sure that it will be an even swoop across the top when you cut out the pattern or you might have a hard time sanding it later. I make sure the center curve fits the smallest wheel I have (2")
Draw a line from the widest point straight up to the top of the sheath. This will be the pattern for the welt. Here I've drawn that in in blue so you can see it better. Don't cut it out yet, we'll do that after transferring the bigger pattern to the leather.
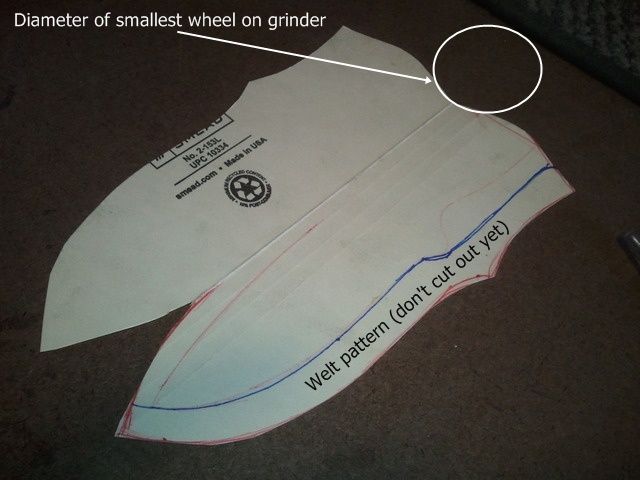
If you have to bring two cuts together in a 'V', put a small hole that you can cut out from so the leather doesn't split later.
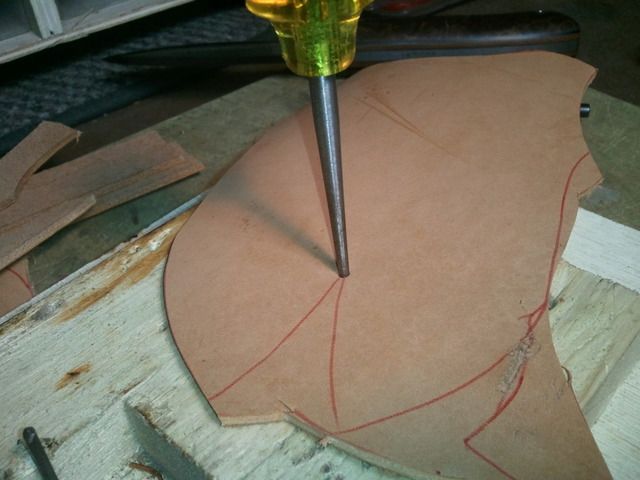
Last edited: