BRad704
Well-Known Member
I started with a piece of 5160, 1/4" thick, about 1x5 (or so)...
Using a rosebud on our cutting torch, heated it up to orange and used a 5lb hammer to work it out. As I was hammering, I began to understand how different angles and different strikes were moving the metal differently, and what I got is actually just what I was going for.
HT was done again with the torch, and once it was non-magnetic, quenched in vegetable oil. Tempered 2 - 90 minute cycles at 375F. This blade might not pass the ABS test, but it was a great proof of concept for me.
Now I have to decide how to finish the handle for it. I am thinking a cherry wood that mirrors the curve of the blade, and using a copper wire wrap at the top and bottom of the handle as an accent.
My uploads from my phone aren't working too well, so I'll add the other pics as soon as I can... About 15 minute on a 220 belt will have the blade ready to sharpen, and I am leaving as much "character" as I can in this blade...
Using a rosebud on our cutting torch, heated it up to orange and used a 5lb hammer to work it out. As I was hammering, I began to understand how different angles and different strikes were moving the metal differently, and what I got is actually just what I was going for.
HT was done again with the torch, and once it was non-magnetic, quenched in vegetable oil. Tempered 2 - 90 minute cycles at 375F. This blade might not pass the ABS test, but it was a great proof of concept for me.
Now I have to decide how to finish the handle for it. I am thinking a cherry wood that mirrors the curve of the blade, and using a copper wire wrap at the top and bottom of the handle as an accent.
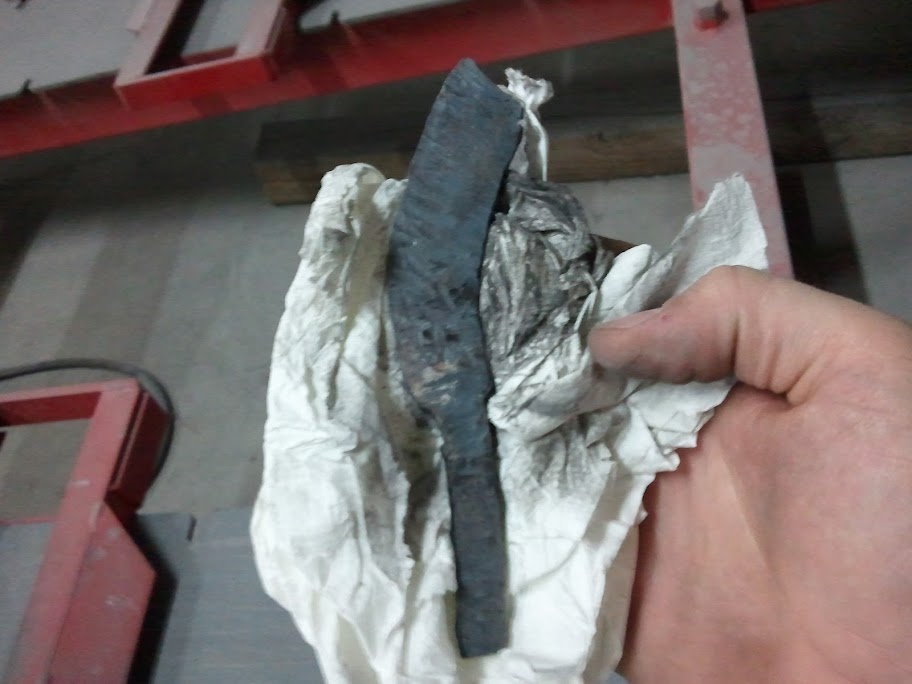
My uploads from my phone aren't working too well, so I'll add the other pics as soon as I can... About 15 minute on a 220 belt will have the blade ready to sharpen, and I am leaving as much "character" as I can in this blade...