RickA
Well-Known Member
Hi Everyone
When I made the knife for my boss a couple of months back I tried out dovetailed bolsters for the first time. I used a friends little chinese (Ryobi) belt/disc grinder combo and it did the job, however for long term use with bolsters, flattening and squaring handle scales etc I decided to build my own double ended disc grinder. Similar to my 300mm/12" contact wheel which I made last year, I made my own discs out of 235mm dia Aluminium offcuts from a local Non Ferrous Metals supplier. To make the two discs cost around R180 ~ $18 and a few hours work on a lathe (it's probably not neccessary in the USA, but in South Africa this is a fraction of the price of buying the discs / wheels from a supplier). One of the offcuts was a bit too thin to turn a "hub" so I had to have a boss for the hub welded on.
The motor is a 0.75KW / 1HP 3 phase motor. My KMG style belt grinder and the new disc grinder sit next to each other on the bench and both run off the same VFD (alternately - not at the same time)
I designed and built a swiveling frame to allow the grinder to sit in one fixed position on the bench but still allow me to access both discs from the front. I welded the frame up and painted it last week. Tested it out yesterday and it works like a dream, its definitely going to be a valuable addition to the shop. I would still like to add a horizontal disc grinder with interchangeable discs for quickly and easily changing grits as well as a horizontal "mini wheel grinder" - but those will come in time, for now I need to get back to making knives and not making more machines.
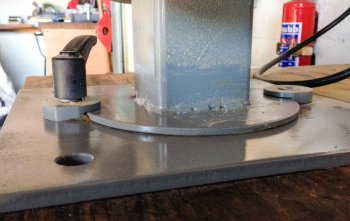
At the end of March we had a bladesmithing hammer-in at our knife club here in Cape Town. We arranged for the chairman of the South African Bladesmiths Association, a full time pro knifemaker and Knifemakers guild member to fly down for the weekend and run the hammer-in. A very good day was had by all and a lot of new bladesmithing converts were created, myself included, as a result of the fun I had on the day I am currently building a small gas forge and have started trawling the local pawn shops, flea markets etc looking for decent old hammers, anvils etc.
When I made the knife for my boss a couple of months back I tried out dovetailed bolsters for the first time. I used a friends little chinese (Ryobi) belt/disc grinder combo and it did the job, however for long term use with bolsters, flattening and squaring handle scales etc I decided to build my own double ended disc grinder. Similar to my 300mm/12" contact wheel which I made last year, I made my own discs out of 235mm dia Aluminium offcuts from a local Non Ferrous Metals supplier. To make the two discs cost around R180 ~ $18 and a few hours work on a lathe (it's probably not neccessary in the USA, but in South Africa this is a fraction of the price of buying the discs / wheels from a supplier). One of the offcuts was a bit too thin to turn a "hub" so I had to have a boss for the hub welded on.
The motor is a 0.75KW / 1HP 3 phase motor. My KMG style belt grinder and the new disc grinder sit next to each other on the bench and both run off the same VFD (alternately - not at the same time)
I designed and built a swiveling frame to allow the grinder to sit in one fixed position on the bench but still allow me to access both discs from the front. I welded the frame up and painted it last week. Tested it out yesterday and it works like a dream, its definitely going to be a valuable addition to the shop. I would still like to add a horizontal disc grinder with interchangeable discs for quickly and easily changing grits as well as a horizontal "mini wheel grinder" - but those will come in time, for now I need to get back to making knives and not making more machines.
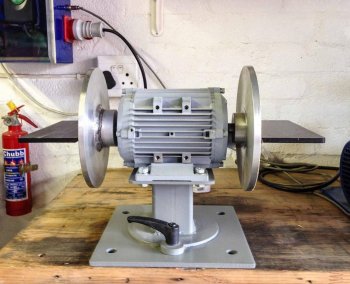
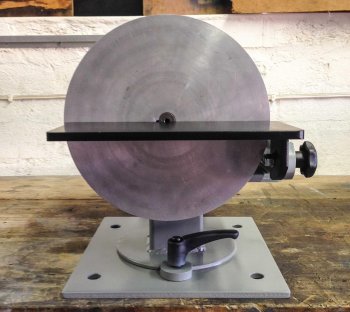
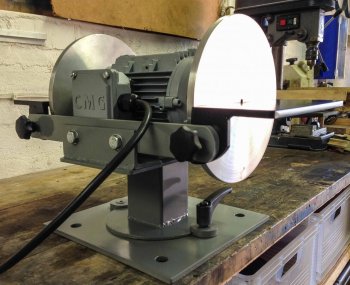
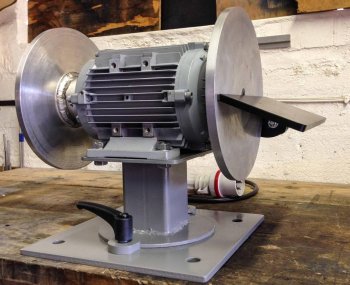
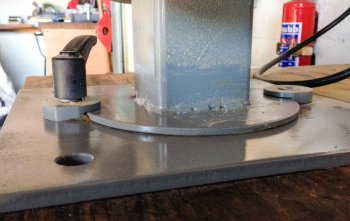
At the end of March we had a bladesmithing hammer-in at our knife club here in Cape Town. We arranged for the chairman of the South African Bladesmiths Association, a full time pro knifemaker and Knifemakers guild member to fly down for the weekend and run the hammer-in. A very good day was had by all and a lot of new bladesmithing converts were created, myself included, as a result of the fun I had on the day I am currently building a small gas forge and have started trawling the local pawn shops, flea markets etc looking for decent old hammers, anvils etc.