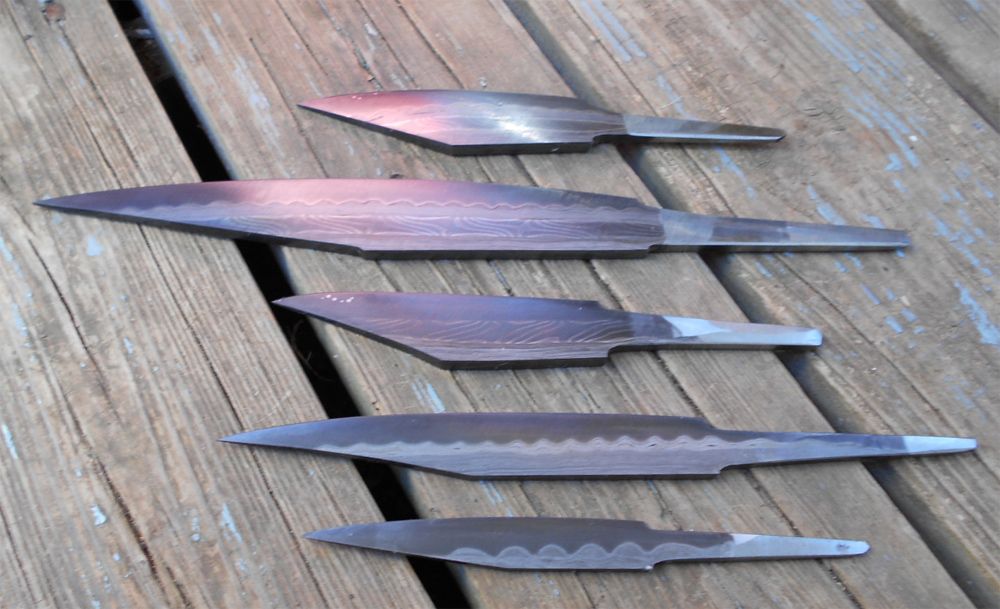
Two of these are commissions, the rest were test pieces and offcuts that somehow became seaxes. The two bottom blades were the experiments in wolf's toothery, one, the smaller of the two had the pattern forged into the wrought iron and ground into the edge bar, the other the pattern was forged into the edge bar and the iron forged into it while the welding took place. Both experiments seemed to work, with no real advantage found to either method, IMO. These are all ground to 120 grit with a test etch before heat-treating.
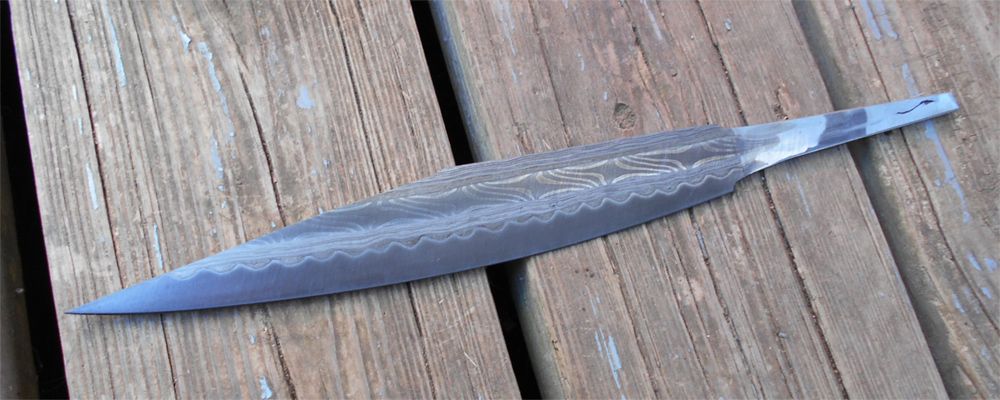
This is the blade that was commissioned, he wanted a 'serrated' weld, after several experiments on how best to do a wolf's tooth, this is the result. It is based on a blade in the Museum of Ireland, I got her pretty close to the original's shape. The blade is approximately 9" long with a 4" tang.
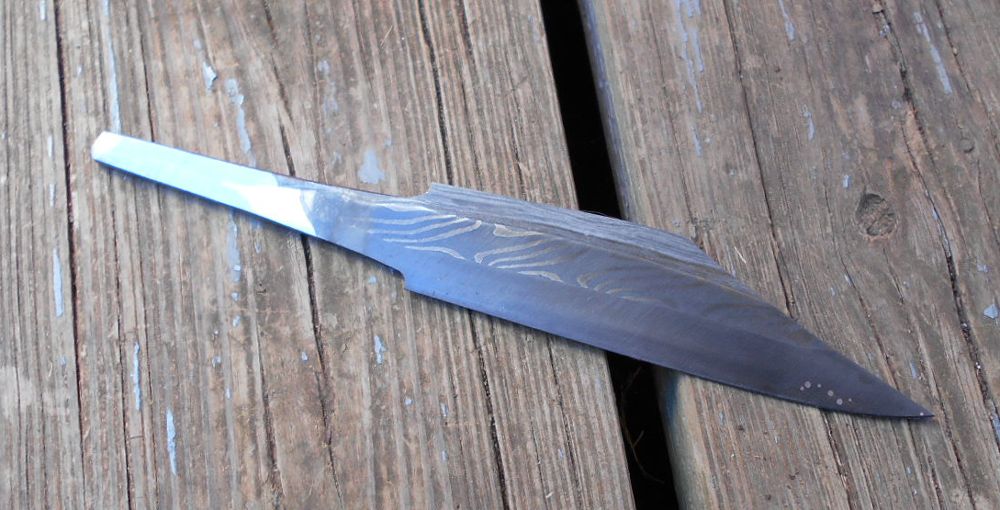
This one is a commission, seems a bit plain after all the wolf's tooth welds but I'm very happy with the shape. The blade is about 4 3/4" long.
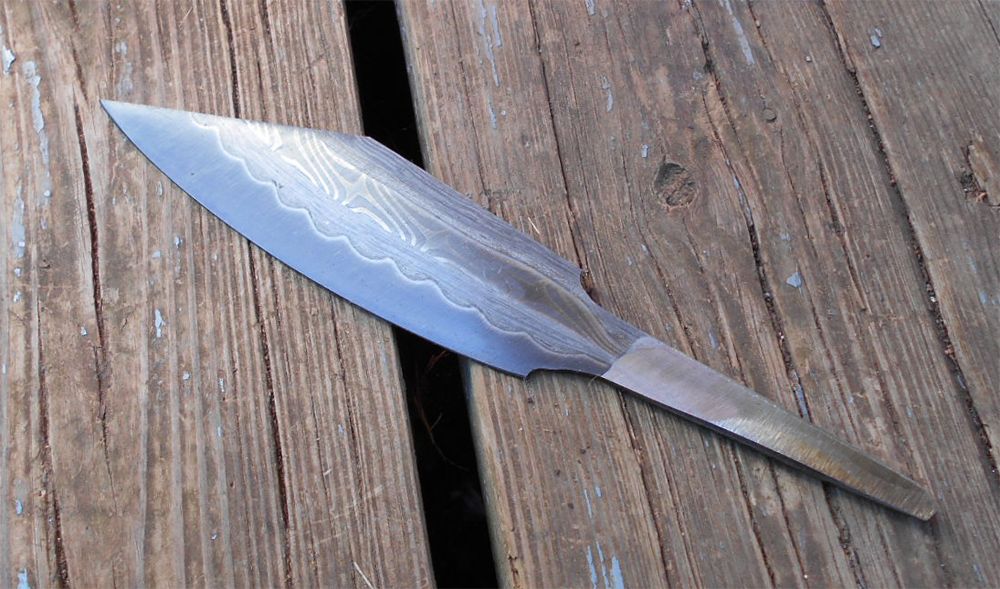
This one was an offcut from the other billet that needed to be dealt with. The wrought I've been using is particularly nasty, but I must admit it is pretty... I suspect it has a fairly high phosphorus content, and it was very obvious even before the blade was etched. It develops a rusty red patina very quickly.
Well, that's what I've been up to lately. Hopefully I'll have some finished seaxes to show in the next few weeks.
Almost forgot to mention, the edge steel is 1095 on the 3 bottom knives, W2 on the 2 on top. The twists are 11 layer 1084 and 15n20.
Last edited: