Frank Hunter
Well-Known Member
This was a huge job. It was commissioned by a very patient client shortly after Christmas last year and getting it all wrapped up took most of this year to complete.
There are 3 sets of 3 knives, a 3 7/8" skinner, 5" hunter and 6" chisel point tanto, each set with a different handle material selection. The hunter and skinner sets are .155 CPM 154CM, all with mitered 304 stainless bolsters. The tantos are 440C, roughly .190 thick, and that steel showed such a wicked linear grain with carbides flecking out that I was unable to mirror polish it, so the whole batch has a bright buffed finish versus a true mirror. Between the finish fiasco, etchant issues, and the steel being surfaced twice as I obtained a surface grinder midway through the project and some other shenanigans I have around 175 hours in the whole batch.
Comments are welcome!
Black/Silver Dymondwood Laminate
Black/Hunter Orange G10
Bone Imistag from USAknifemaker.
There are 3 sets of 3 knives, a 3 7/8" skinner, 5" hunter and 6" chisel point tanto, each set with a different handle material selection. The hunter and skinner sets are .155 CPM 154CM, all with mitered 304 stainless bolsters. The tantos are 440C, roughly .190 thick, and that steel showed such a wicked linear grain with carbides flecking out that I was unable to mirror polish it, so the whole batch has a bright buffed finish versus a true mirror. Between the finish fiasco, etchant issues, and the steel being surfaced twice as I obtained a surface grinder midway through the project and some other shenanigans I have around 175 hours in the whole batch.
Comments are welcome!
Black/Silver Dymondwood Laminate
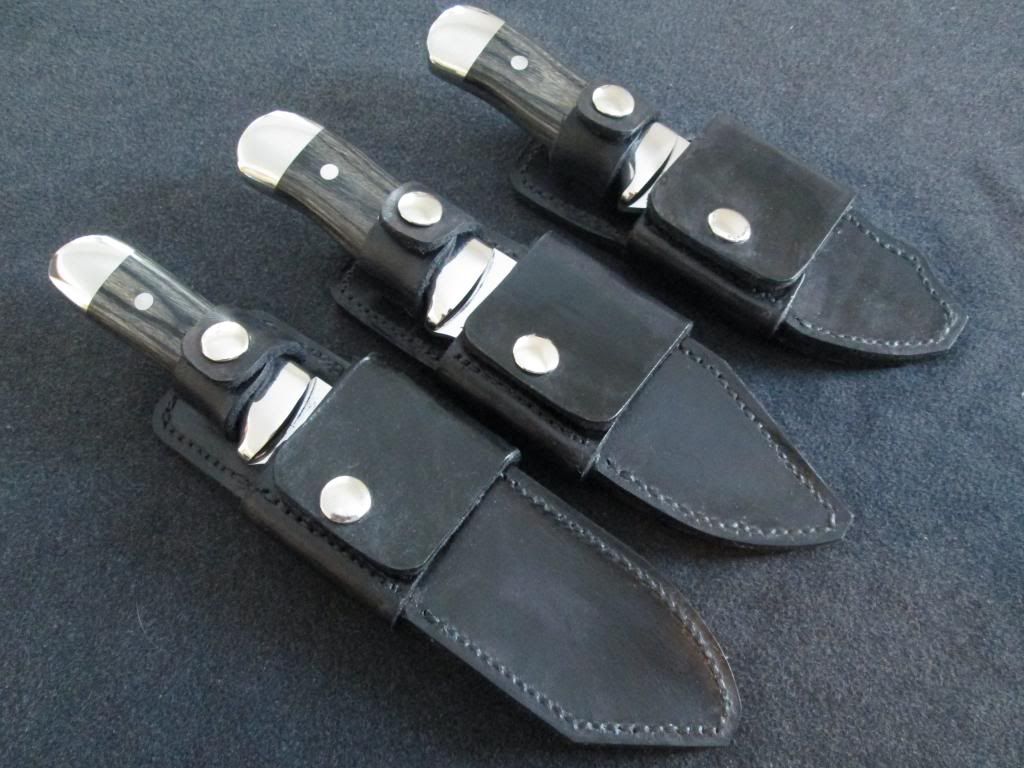
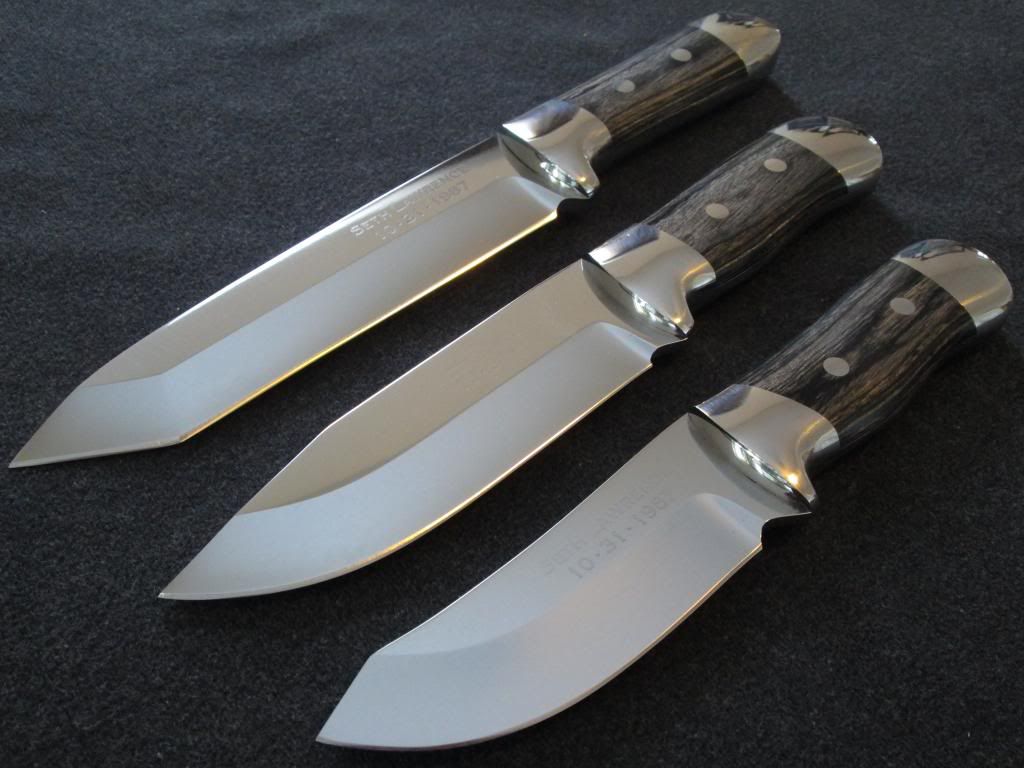
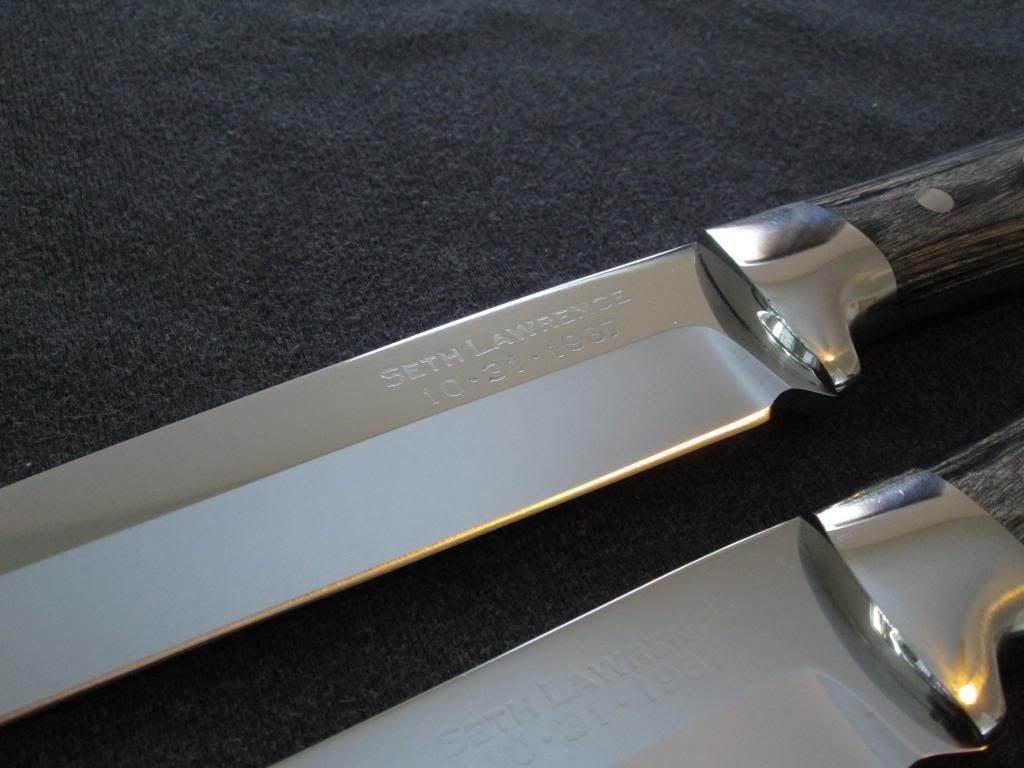
Black/Hunter Orange G10

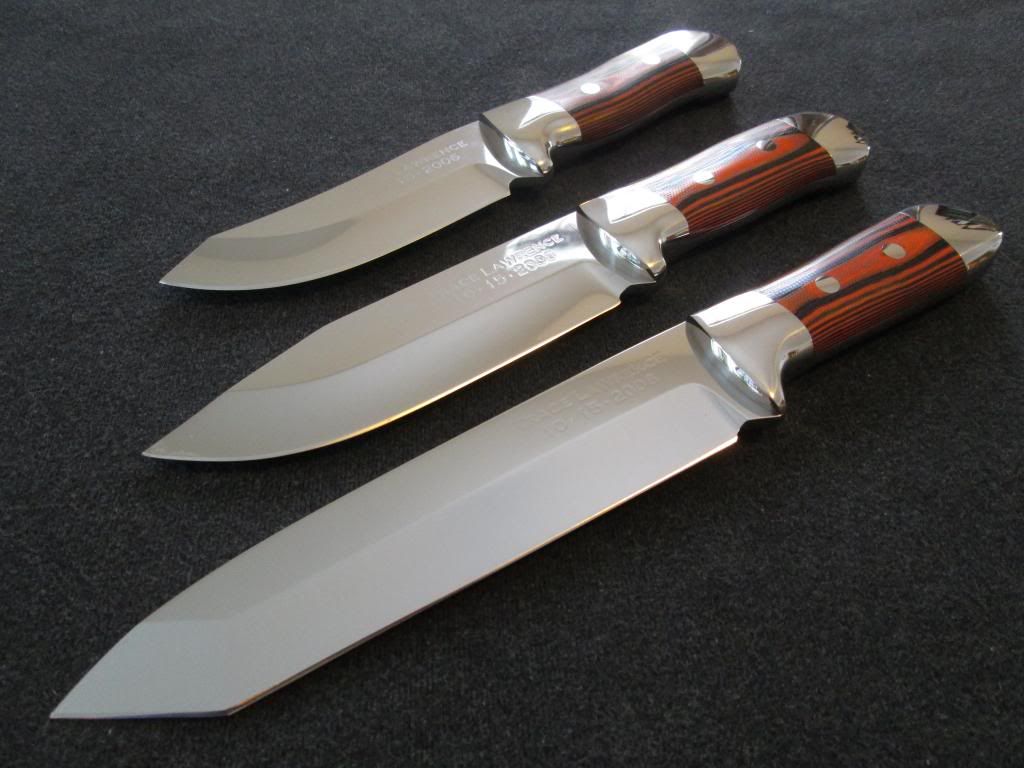
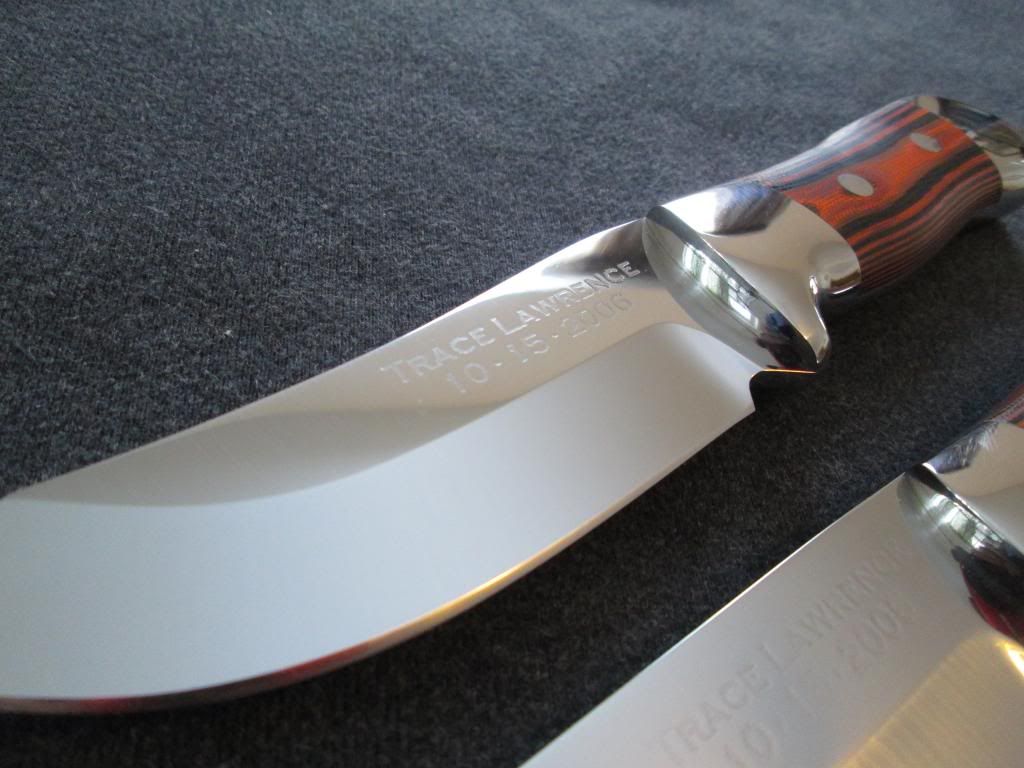
Bone Imistag from USAknifemaker.
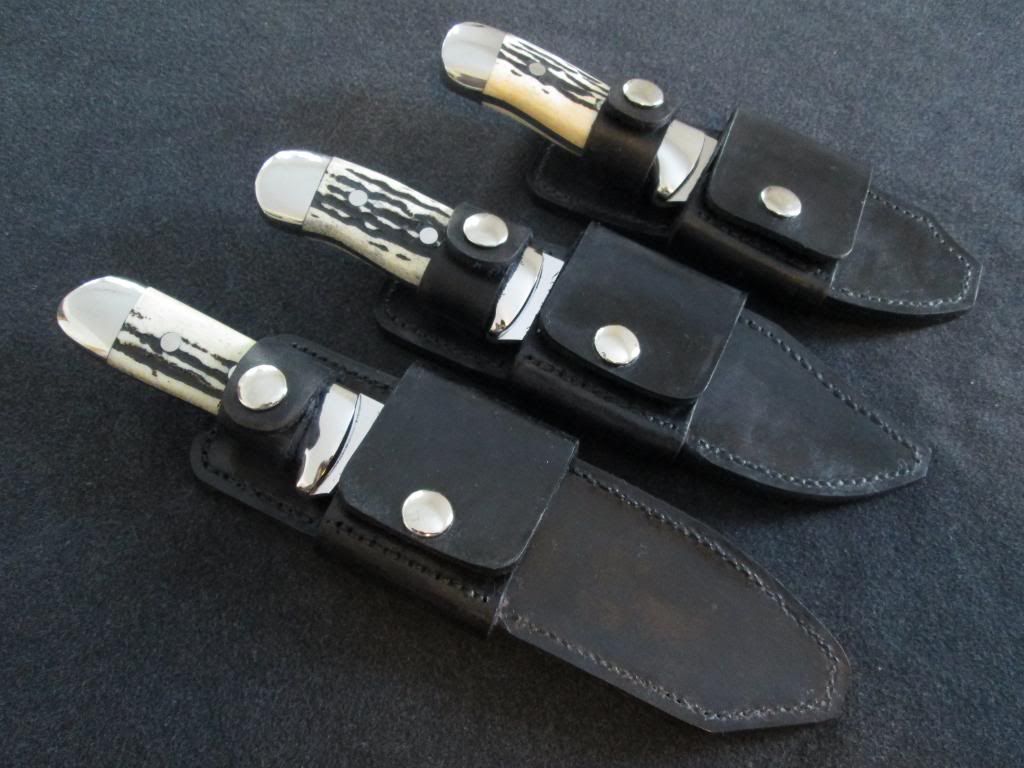
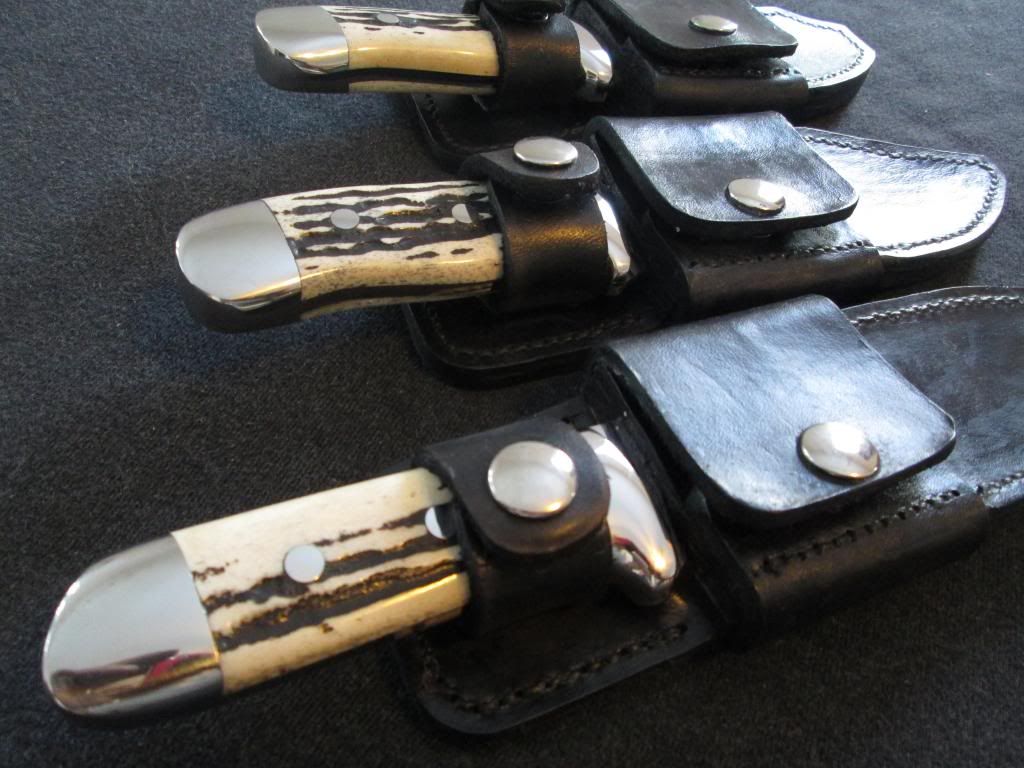
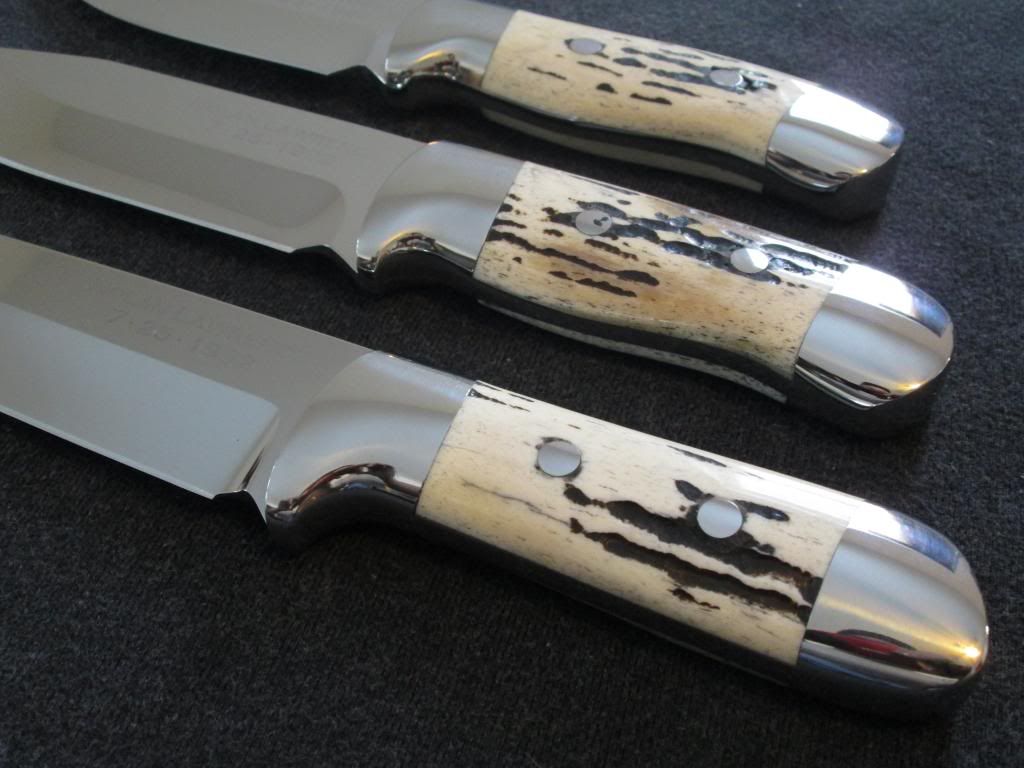
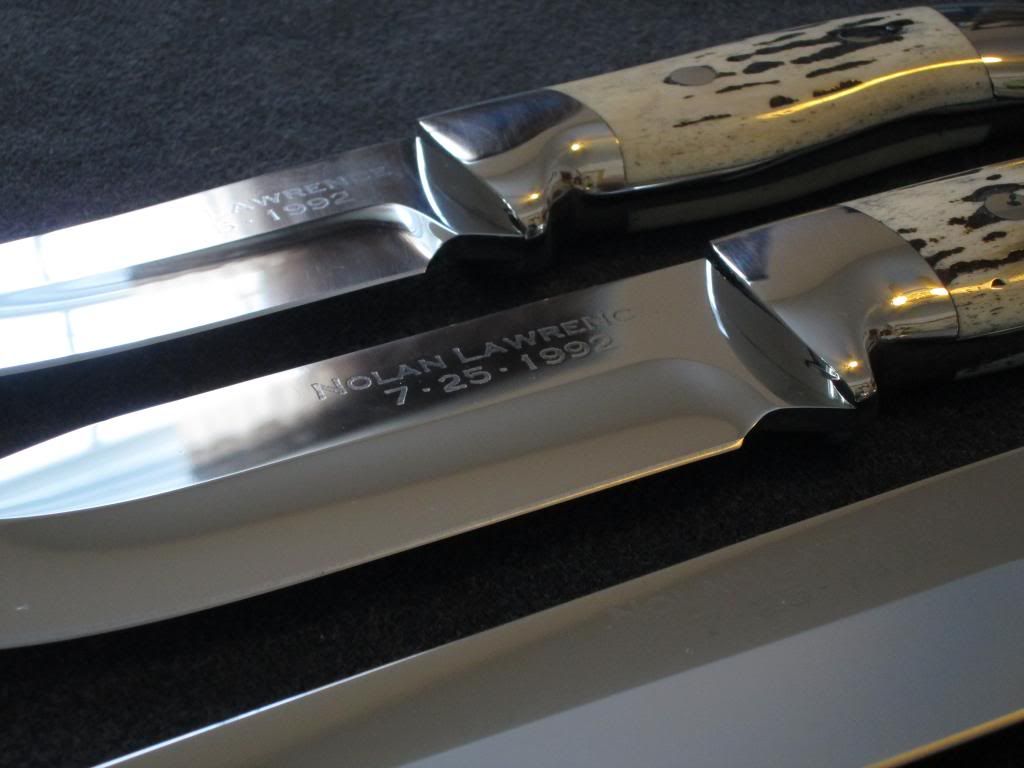