JRB Blades
Well-Known Member
Starting a thread to show the progress on my small batch run of frame locks. Making 7 knives total. They will all have .125" MagnaCut blades finished to about 63-64 Rockwell. I'll have 4 of the Gator model with .135" titanium scales and 3 of the Fighter model with .140" scales. I'm gonna try to include pictures and details of what/why I'm doing certain things.
Nothing too exciting yet... First step was to glue up my blade templates and cut them out on the band saw and then rough grind them to shape with an 80 grit belt. I left some meat around the template so that once I get the scales to their final shape, I can install the blade and make sure that my lines are flush between the blade and the scales in certain areas. It'll make more sense once I get to that point in the build. Tonight I'll refine the shape with a 120 grit belt and try to get the pivot holes drilled and reamed.
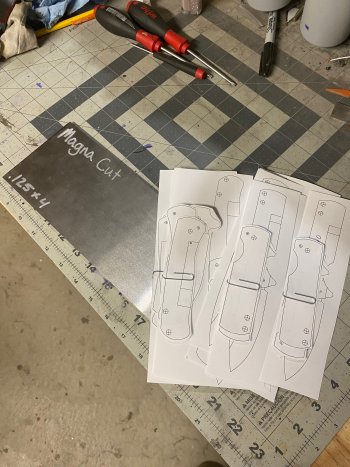
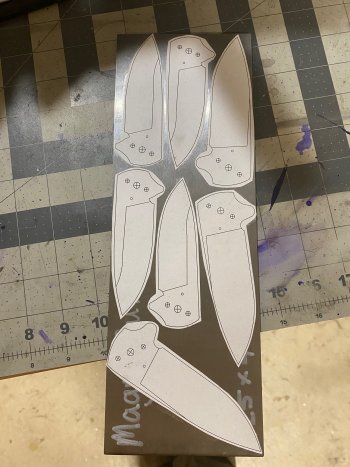
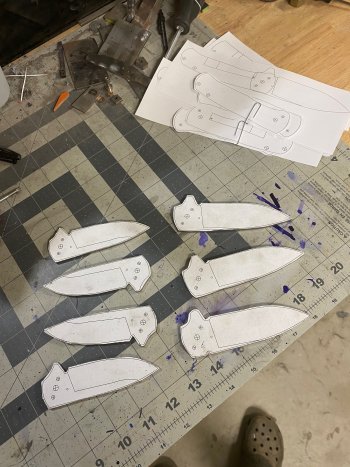
Nothing too exciting yet... First step was to glue up my blade templates and cut them out on the band saw and then rough grind them to shape with an 80 grit belt. I left some meat around the template so that once I get the scales to their final shape, I can install the blade and make sure that my lines are flush between the blade and the scales in certain areas. It'll make more sense once I get to that point in the build. Tonight I'll refine the shape with a 120 grit belt and try to get the pivot holes drilled and reamed.
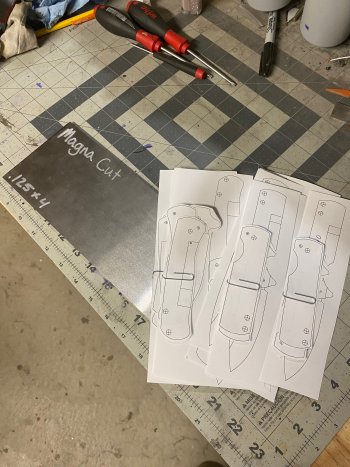
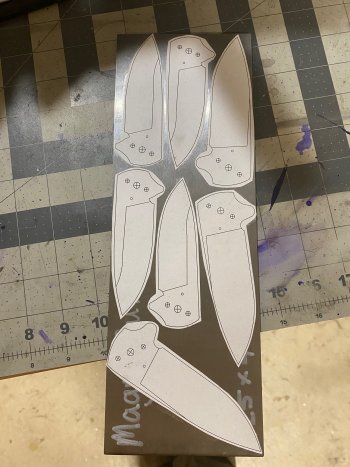
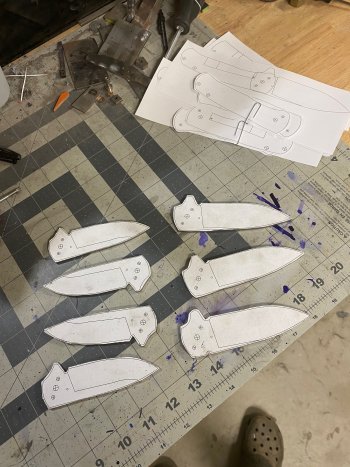