Awoke to 10* temps this a.m., didn't think I'd get any shop time in in that refrigerator of a shop. But, nature was kind to me and we hit the mid-forties, so time to finish prepping it, then spot weld the edges all around.
Wire brushed the slag off, time to heat things up.
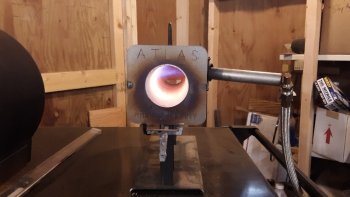
Love hearing that thing go whoomph!
I'm always amazed by how fast, hot, and economical to run this little forge is.
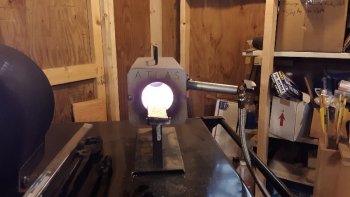
(I think his big brother just to his left gets jealous).
I heat it up to just past orange, when it is starting to almost go white, but not quite, I start tap dancing the hammer all over it. When the steel starts to cool, heading back to a bright orange, I put it back in the forge. I work from one end to the other in a three or four inch long area at a time, always overlapping the last area worked. You know it is welding the pieces because you can "feel" it as you are tapping along. You don't want to hit as hard as you do when you are forging the knife shape.
Once I work down the entire length, I flip it end to end and start over, working the whole thing again. I do this three times.
If you have welded the whole thing, you can "feel" the billet getting "stiffer", one solid piece now (hard to put it into words).
At this point, I shut down the forge, let the billet cool to around 800-900* and let it sit in the cooling forge until around 400-500*.
Then I remove from the forge, wire brush it, and let it sit overnight. Next time I will start forging the blade
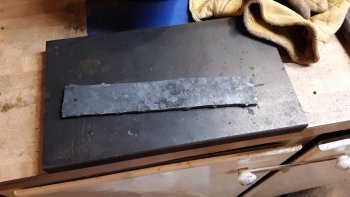