Doug Lester
Well-Known Member
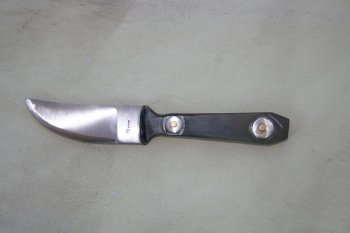
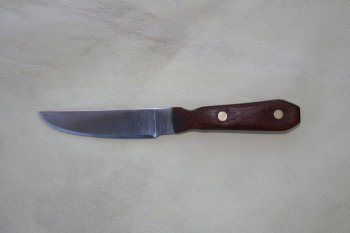
The second is a straight spined blade with leopard wood scales attached with brass cutler's rivets. The scales had previously been treated with Nelsonite but that didn't prevent it from taking four coats of boiled linseed oil. It has an OAL of 8 1/2" with a 4 1/2" blade that is 1" wide at the plung line and 3/16" thick at the ricasso.
Both were forged from 3/4" 52100 round bar. They were normalized three times after forging and again after the rough grind. They were also austempered at 430 degrees for two hours followed by a single cycle of in the oven at 425 degrees. They were given a satin finish.
Doug Lester