DonL
Well-Known Member
Okay, I didn't start taking pics at first because I had no intention of making this a WIP! But since Boss asked for 'em, here it is. (plus it doesn't hurt that he's willing to put us in a drawing for some goodies)
I want to start off by saying that this started off as a hair-brained idea of mine. Follow it at your own risk because I have no idea if it'll work or not. I'm in need of a decent heat treating set up. My 1 gallon paint can forge is a year old and it's really hard to get consistent results from it, even with a digital temp gauge and Tempilstiks! Ever hold a knife blade so it can "soak" all the time moving it back and forth so it doesn't get too hot in one spot? I nearly pulled the trigger on the last Sugar Creek Kiln on ebay, but decided at the last minute to save my money and put it on my LB-1000. So this is what I came up with as an alternative.
I looked and looked around locally for some type of metal cyclinder object to make my heat treat furnace. I looked at examples of other furnaces/kilns on the web and liked the idea of how salt pots worked. Eventually I bit the bullet and bought a 15 gallon metal drum off of ebay. $45 shipped. It's military surplus and I sure wish I knew what they packed in these things! Inside was mostly green foam with a small opening in the middle. The drum is a little over 15" in diameter and about 22" tall. Since I don't plan on making anything larger than a 6 or 7 inch camp knife, this should be tall enough.
My plan called for putting a 4 to 5 inch pipe in the center of the barrel as the Mother of All Heat Treat Mufflers. This way I should get even heat, or so I'm thinking! I happen to ask my neighbor if there was a good junk yard around. He wanted to know what I needed and I told him a 4 or 5 inch length of pipe. He told me to come down to his house and take a look at some pipe in his backyard. WooHoo! He had a short section of 4 1/2" pipe that was cut to nearly the perfect length! Schedule 80 it appears! Plus, he GAVE it to me! FREE STUFF! I love it!
Here's my thought process. I'd use a 1 1/2" black iron coupling for the burner holder at the bottom of the drum. Near the top, I'd put an exhaust consisting of a 1 1/2" coupling.
I went to Lowe's and bought a Lennox 1 1/2" hole saw for my drill to drill out the holes for the black iron couplings. Okay, I knew better but my brain wasn't engaged when I did this. A 1 1/2" hole saw drills a 1 1/2" hole. A 1 1/2" black iron nipple has an INSIDE DIAMETER of 1 1/2" (or just a tad bigger). Needless to say, I had to break out the Dremel with the little metal cut off saw wheel and cut away to make the bottom hole larger. For the top exhaust, I went with a 1 1/4" coupling that fit the hole the hole saw blade made with little filling.
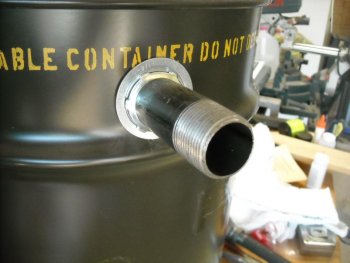
My plan was to line the inside of the drum and the lid with 1" inswool and then coat it with Satanite and ITC 100. Don't ask me why two refractory cements, just seemed like a good thing to do. Maybe I read it someplace once, I dunno. I'm kinda like that sometimes, over kill to the Nth degree!
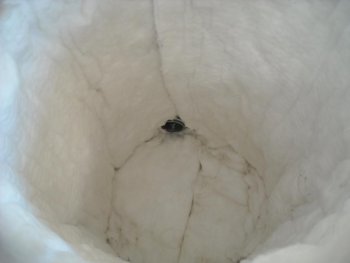
For the burner holder, I drilled 3 - 1/4" holes around the outside with the intention of tapping them 1/4-20. Again, brain not engaged because a 1/4-20 bolt will not get anywhere tight if the hole is drilled with a 1/4" bit! Gotta use the right bit and tap. Of course I knew that in advance, I just got into a hurry and let it slip my mind. So after that debacle, I drilled 3 CORRECT sized holes and tapped them. These bolts will hold the burner into place.
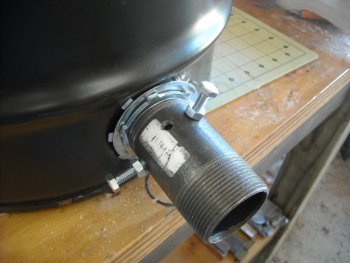
I then cut my inswool to fit the inside of the drum and the bottom of the lid. I wanted my first coat to go on real thin and then the next coat will be a little thicker. I got that done this morning. All the pieces are sitting out and drying. It's suppose to get near 90 here today, so I'm hoping by tomorrow they'll be dry enough for the 2nd coat.
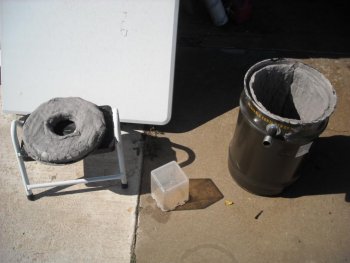
Feel free to ask questions or make suggestions. This is all new to me (and my first WIP!) and I'd appreciate hearing your comments and recommendations.
I want to start off by saying that this started off as a hair-brained idea of mine. Follow it at your own risk because I have no idea if it'll work or not. I'm in need of a decent heat treating set up. My 1 gallon paint can forge is a year old and it's really hard to get consistent results from it, even with a digital temp gauge and Tempilstiks! Ever hold a knife blade so it can "soak" all the time moving it back and forth so it doesn't get too hot in one spot? I nearly pulled the trigger on the last Sugar Creek Kiln on ebay, but decided at the last minute to save my money and put it on my LB-1000. So this is what I came up with as an alternative.
I looked and looked around locally for some type of metal cyclinder object to make my heat treat furnace. I looked at examples of other furnaces/kilns on the web and liked the idea of how salt pots worked. Eventually I bit the bullet and bought a 15 gallon metal drum off of ebay. $45 shipped. It's military surplus and I sure wish I knew what they packed in these things! Inside was mostly green foam with a small opening in the middle. The drum is a little over 15" in diameter and about 22" tall. Since I don't plan on making anything larger than a 6 or 7 inch camp knife, this should be tall enough.
My plan called for putting a 4 to 5 inch pipe in the center of the barrel as the Mother of All Heat Treat Mufflers. This way I should get even heat, or so I'm thinking! I happen to ask my neighbor if there was a good junk yard around. He wanted to know what I needed and I told him a 4 or 5 inch length of pipe. He told me to come down to his house and take a look at some pipe in his backyard. WooHoo! He had a short section of 4 1/2" pipe that was cut to nearly the perfect length! Schedule 80 it appears! Plus, he GAVE it to me! FREE STUFF! I love it!
Here's my thought process. I'd use a 1 1/2" black iron coupling for the burner holder at the bottom of the drum. Near the top, I'd put an exhaust consisting of a 1 1/2" coupling.
I went to Lowe's and bought a Lennox 1 1/2" hole saw for my drill to drill out the holes for the black iron couplings. Okay, I knew better but my brain wasn't engaged when I did this. A 1 1/2" hole saw drills a 1 1/2" hole. A 1 1/2" black iron nipple has an INSIDE DIAMETER of 1 1/2" (or just a tad bigger). Needless to say, I had to break out the Dremel with the little metal cut off saw wheel and cut away to make the bottom hole larger. For the top exhaust, I went with a 1 1/4" coupling that fit the hole the hole saw blade made with little filling.
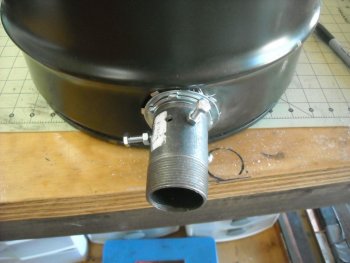
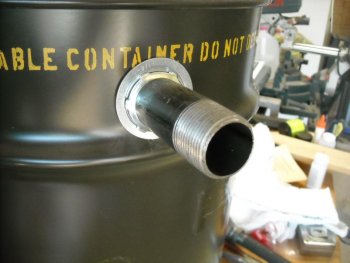
My plan was to line the inside of the drum and the lid with 1" inswool and then coat it with Satanite and ITC 100. Don't ask me why two refractory cements, just seemed like a good thing to do. Maybe I read it someplace once, I dunno. I'm kinda like that sometimes, over kill to the Nth degree!
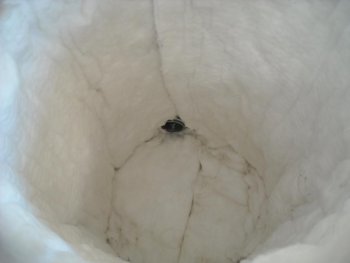
For the burner holder, I drilled 3 - 1/4" holes around the outside with the intention of tapping them 1/4-20. Again, brain not engaged because a 1/4-20 bolt will not get anywhere tight if the hole is drilled with a 1/4" bit! Gotta use the right bit and tap. Of course I knew that in advance, I just got into a hurry and let it slip my mind. So after that debacle, I drilled 3 CORRECT sized holes and tapped them. These bolts will hold the burner into place.
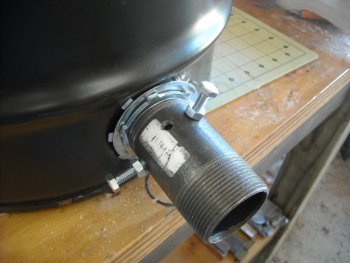
I then cut my inswool to fit the inside of the drum and the bottom of the lid. I wanted my first coat to go on real thin and then the next coat will be a little thicker. I got that done this morning. All the pieces are sitting out and drying. It's suppose to get near 90 here today, so I'm hoping by tomorrow they'll be dry enough for the 2nd coat.
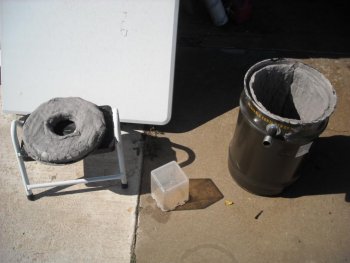
Feel free to ask questions or make suggestions. This is all new to me (and my first WIP!) and I'd appreciate hearing your comments and recommendations.
Last edited: