Bruce Bump
Forum Owner-Moderator
Our own Josh has been doing a great job keeping track of all these WIPs and we all appreciate him more than he knows. Thanks Josh!!
Its time I contributed to this library of tutorials so here is a pictorial and some explaination of what I do to make a Gents Bowie guard, spacer, frame, liners, rear bolsters and ivory handle scales. This method works good for me with my tools but I cant see any reason why you guys couldn't adapt it also. I do have a milling machine that helps tremendously for cutting the slot in the guard but you could do the same slot with a drill press and connect the holes with a round and flat files. I didnt always have a milling machine you know.
I believe all knives should start with a drawing that shows all the parts in the knife. This drawing should be to actual size and should be as exact as possible. Its easy to erase and draw the knife again and again but not so easy after it is cut out of steel. This drawing will be the "blueprint" for the entire construction process so make it look right on paper. One trick to designing a knife is to draw it at night and look at it in the morning. Many times you will see what it needs to improve the design. I use an art drawing book and keep the drawings for future repeat business.
This blade is one I made a few months ago and I'm using this drawing as the handle. Notice it has the guard, spacer, frame and the rear bolsters drawn now. I'm going to use 416 stainless steel for all these parts. Later it will get stainless liners and a pair of nice mammoth ivory scales.
I like 416 stainless because it wont rust on a user knife. Many times I use mild steel especially if it will be hot blued but unless the owner knows to use gun oil on the frame and guard it can rust easily from sweaty hands.
This guard is forged from a bigger piece of 416 stainless and annealed. 416 likes to be forged hot but needs to be annealed afterward because it air hardens to about 48 rockwell. Thats a bit hard to drill, machine, and way to hard to be engraved. This guard is about 20 rockwell hardness and should be nice to work with.
Notice the detailed drawing especially where the frame goes through the spacer and the guard.
I'll later make some copies of this drawing so I can cut and glue the paper to the steel.
The shoulders need to be square so I use a file guide clamped on and use the belt grinder. Also I like to round the tang because the guard slot will be rounded to match.
Copper is a real "camera hound"
Its time I contributed to this library of tutorials so here is a pictorial and some explaination of what I do to make a Gents Bowie guard, spacer, frame, liners, rear bolsters and ivory handle scales. This method works good for me with my tools but I cant see any reason why you guys couldn't adapt it also. I do have a milling machine that helps tremendously for cutting the slot in the guard but you could do the same slot with a drill press and connect the holes with a round and flat files. I didnt always have a milling machine you know.
I believe all knives should start with a drawing that shows all the parts in the knife. This drawing should be to actual size and should be as exact as possible. Its easy to erase and draw the knife again and again but not so easy after it is cut out of steel. This drawing will be the "blueprint" for the entire construction process so make it look right on paper. One trick to designing a knife is to draw it at night and look at it in the morning. Many times you will see what it needs to improve the design. I use an art drawing book and keep the drawings for future repeat business.
This blade is one I made a few months ago and I'm using this drawing as the handle. Notice it has the guard, spacer, frame and the rear bolsters drawn now. I'm going to use 416 stainless steel for all these parts. Later it will get stainless liners and a pair of nice mammoth ivory scales.
I like 416 stainless because it wont rust on a user knife. Many times I use mild steel especially if it will be hot blued but unless the owner knows to use gun oil on the frame and guard it can rust easily from sweaty hands.
This guard is forged from a bigger piece of 416 stainless and annealed. 416 likes to be forged hot but needs to be annealed afterward because it air hardens to about 48 rockwell. Thats a bit hard to drill, machine, and way to hard to be engraved. This guard is about 20 rockwell hardness and should be nice to work with.
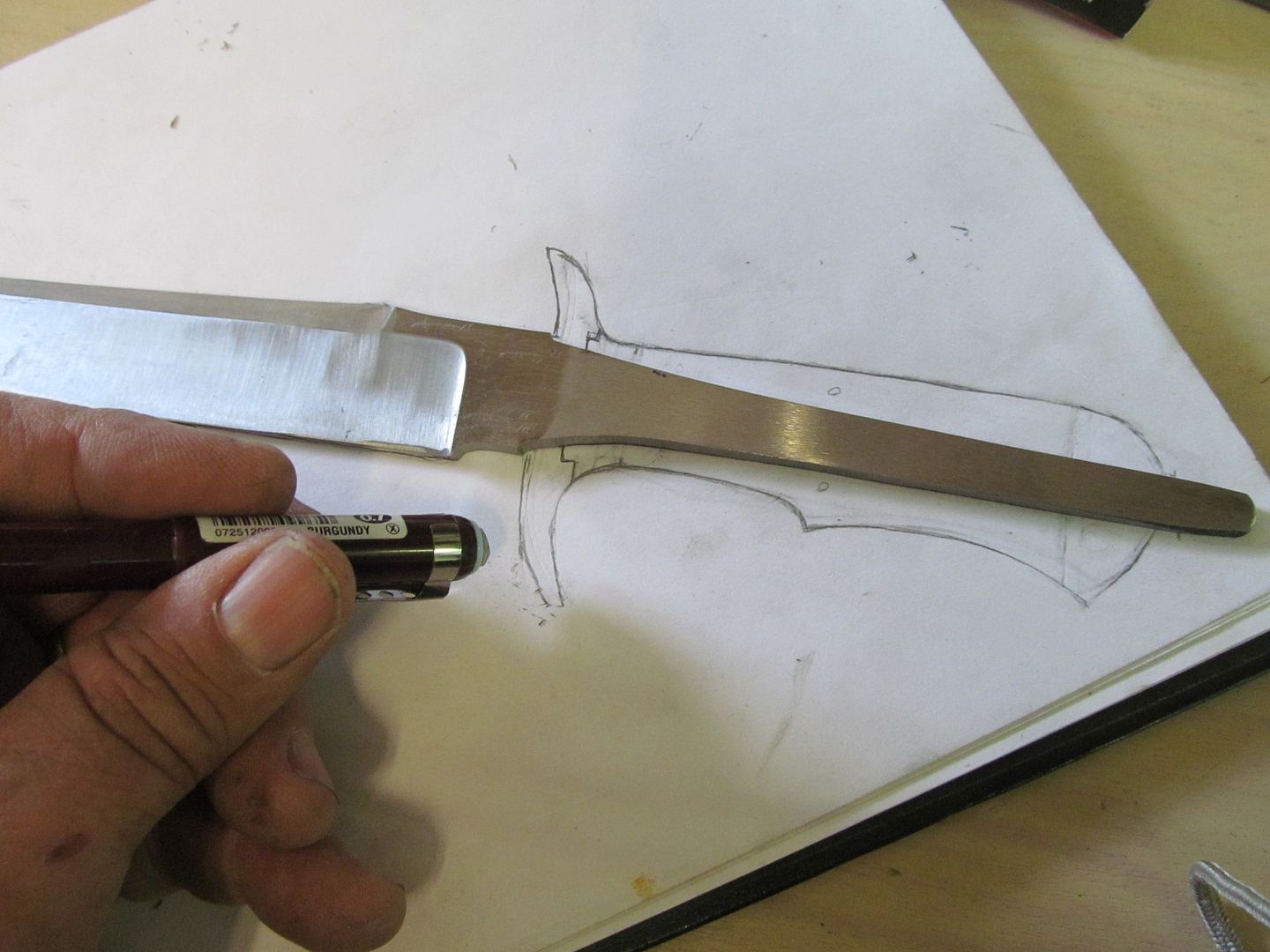
Notice the detailed drawing especially where the frame goes through the spacer and the guard.
I'll later make some copies of this drawing so I can cut and glue the paper to the steel.
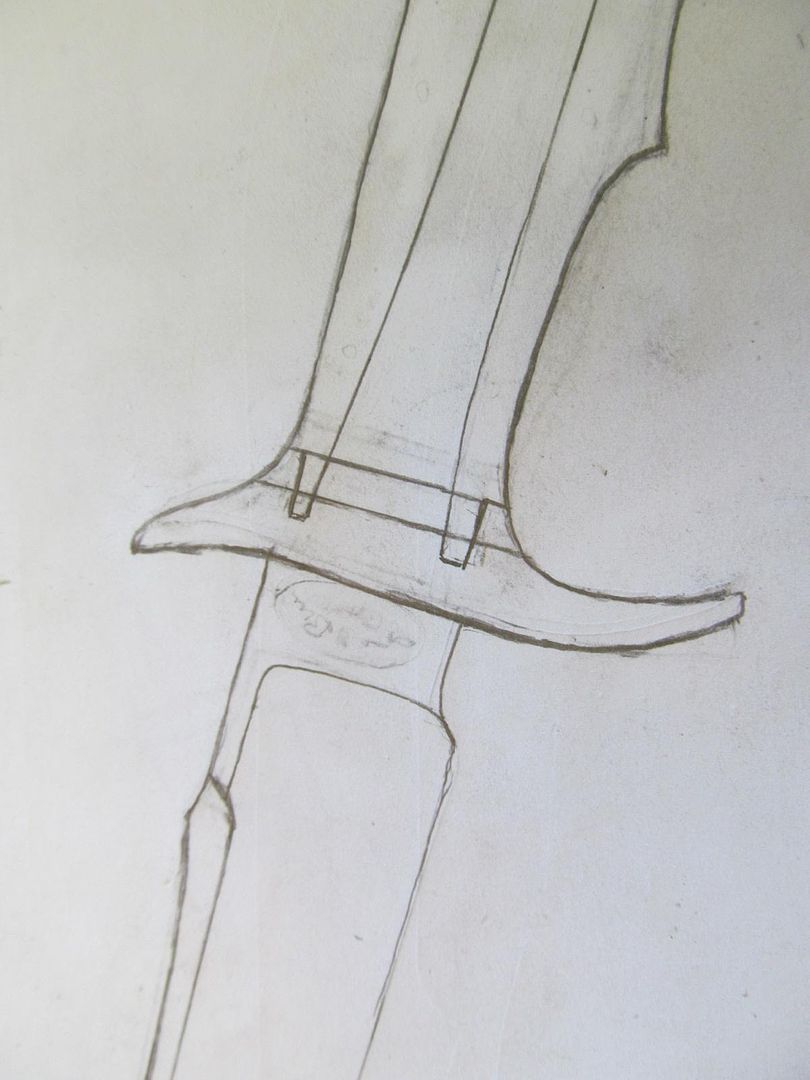
The shoulders need to be square so I use a file guide clamped on and use the belt grinder. Also I like to round the tang because the guard slot will be rounded to match.
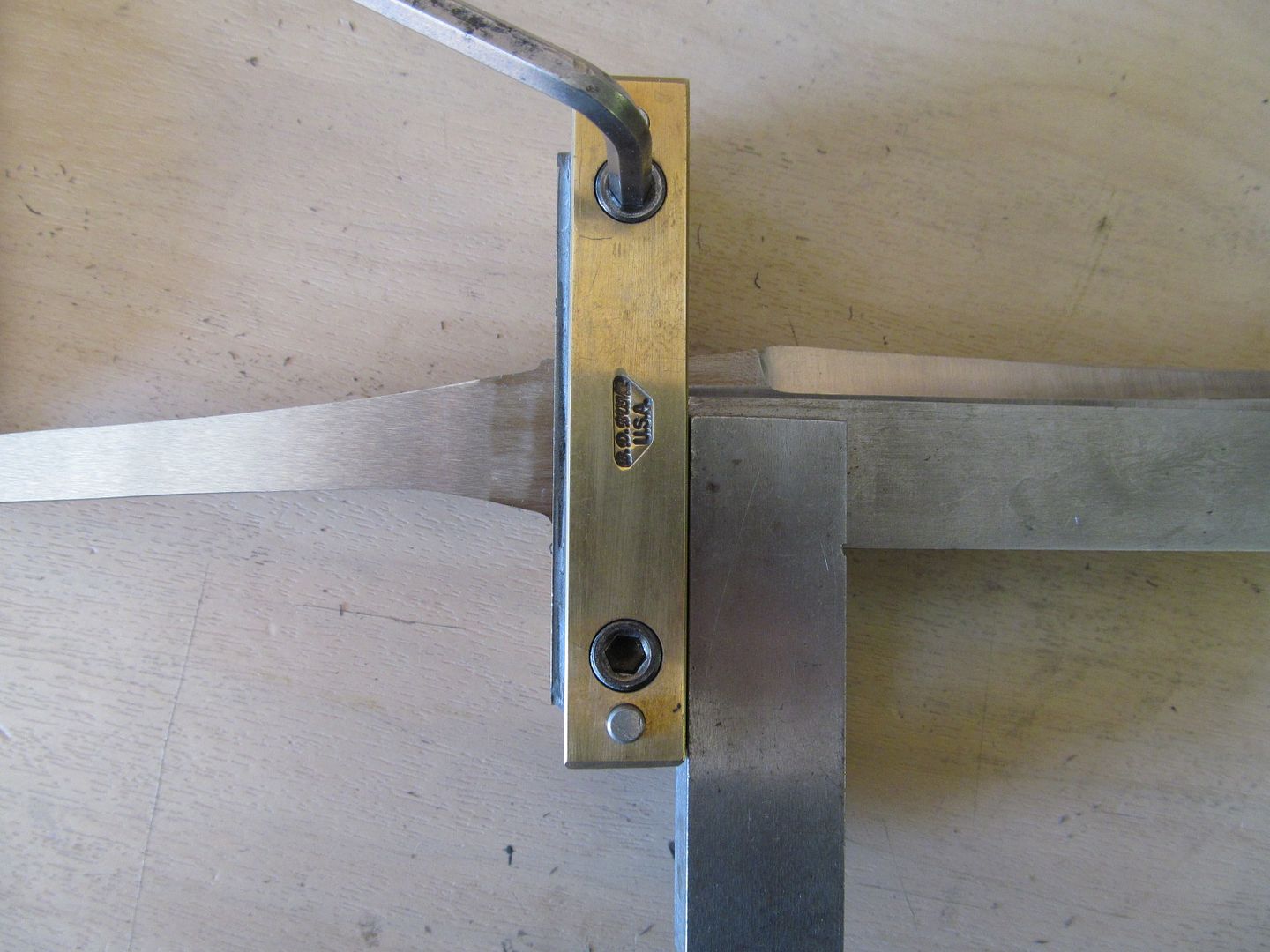
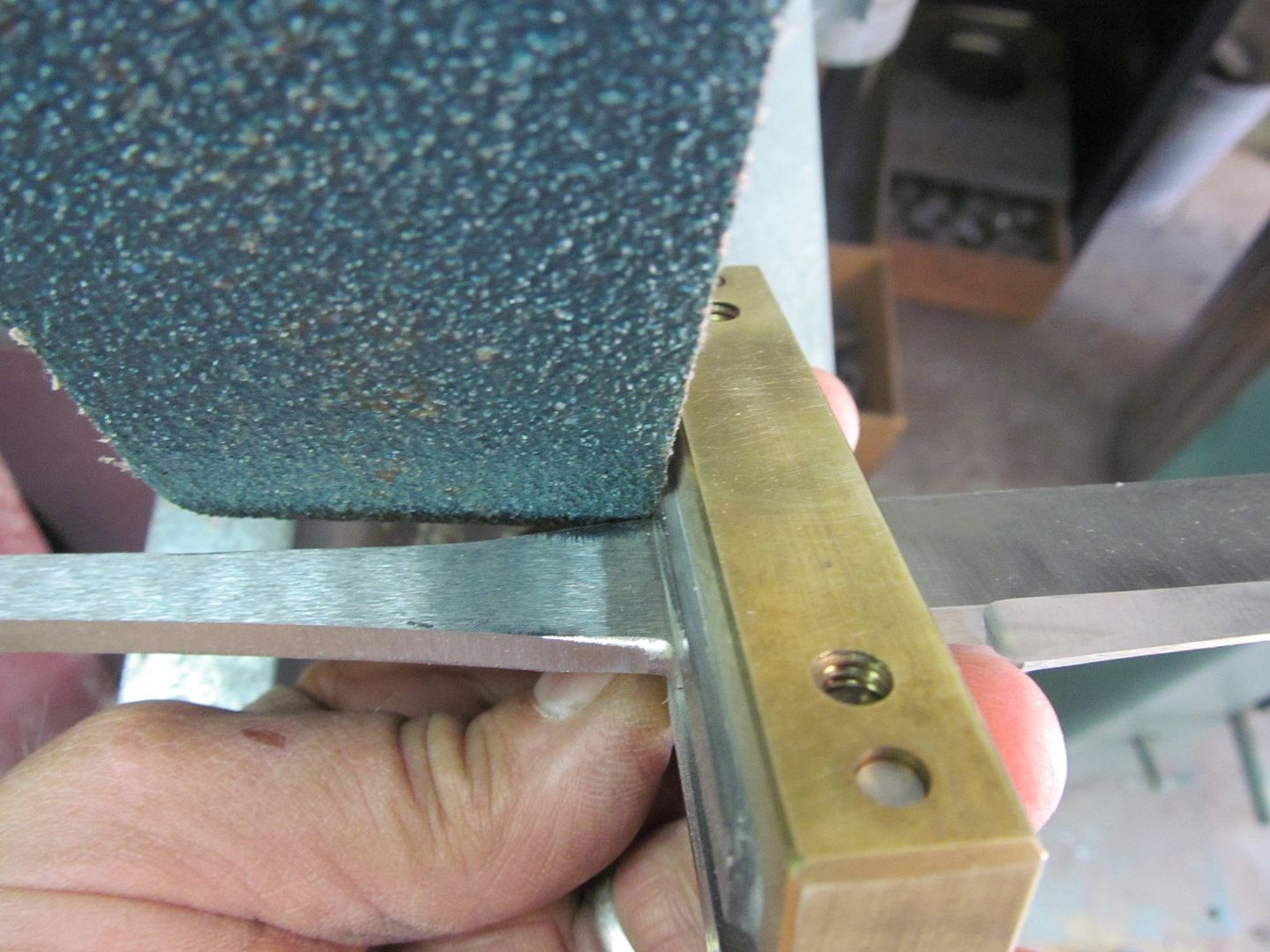
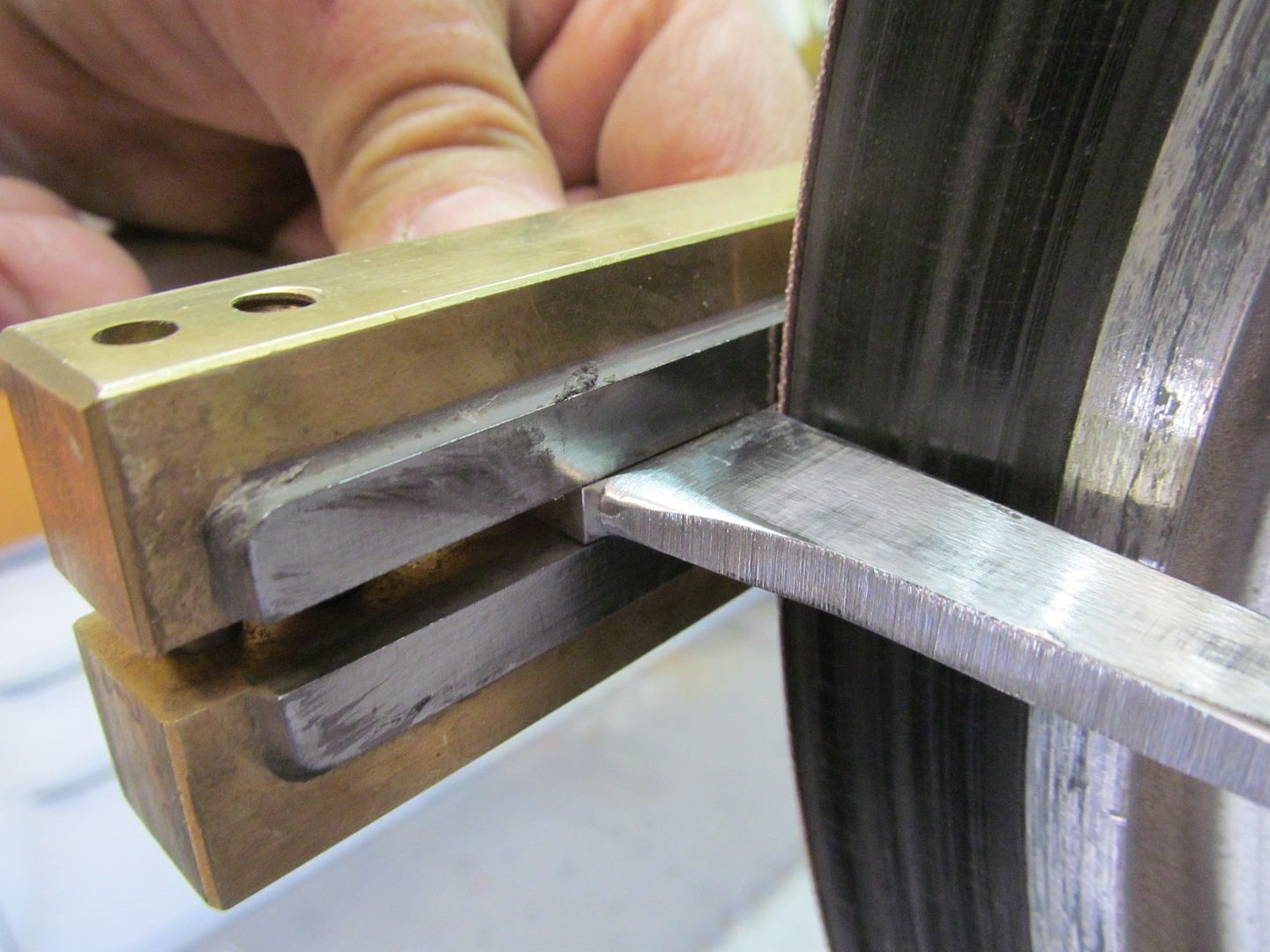
Copper is a real "camera hound"
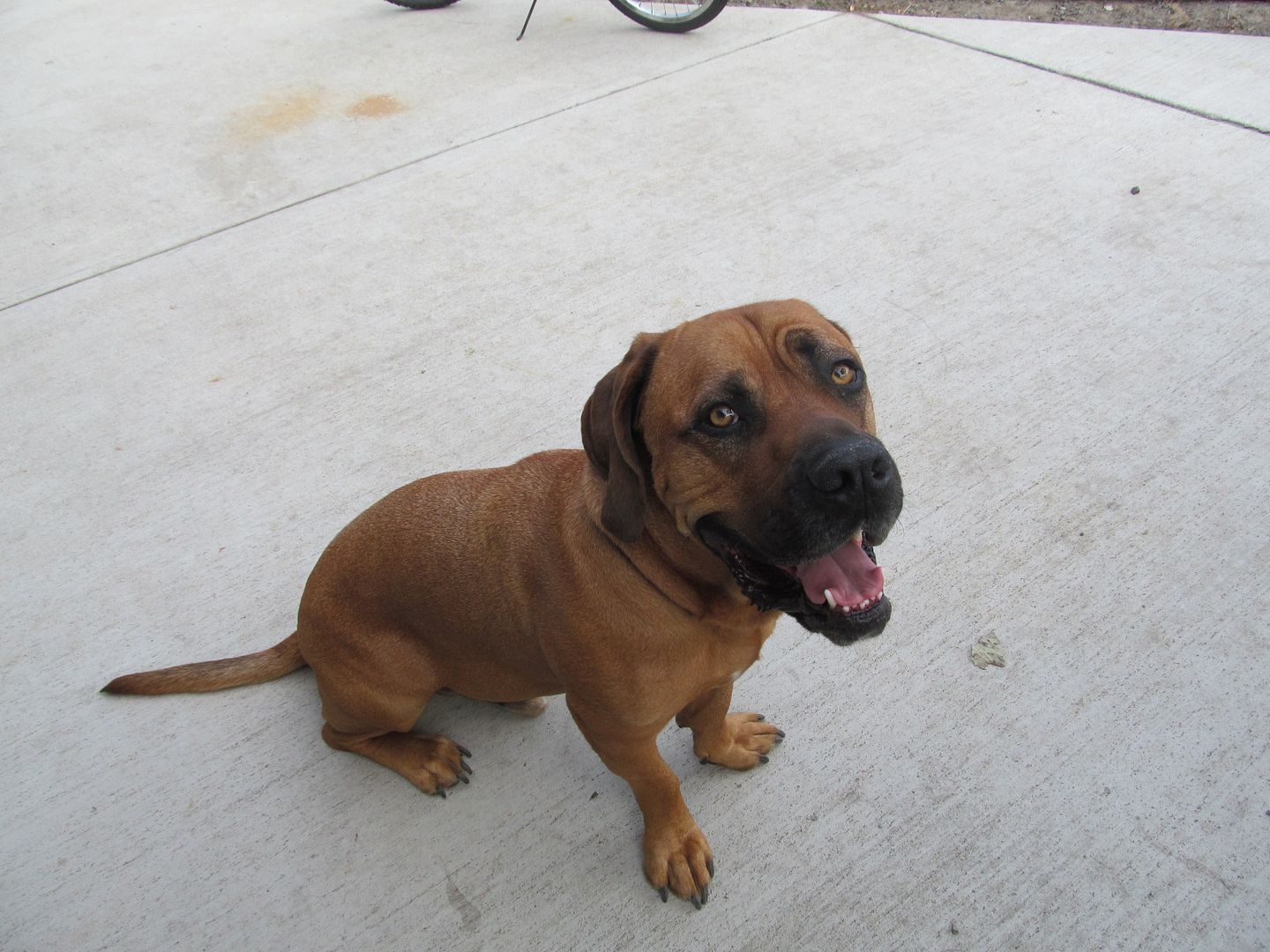