Kurt Krueger
Well-Known Member
Last year I sold a knife to a guy who wanted to give it to his brother as a best-man's gift for his wedding. He loved it, field dressed and butchered a bear and 3 deer with it. Last winter, I asked to see it to evaluate how it was holding up. I was dismayed to find that the edge looked like he'd been cutting music wire and rocks with it. I honed it back up and put a steeper angle on the edge, but something just wasn't right.
I'd always heat treated first and ground second, except on this blade. The steel is AEBL and I heat treat with the blades in a foil pouch to prevent oxygen contact. At first, I though that maybe more oxygen had been trapped in the pouch due to the contour of the primary grinds. The more I thought about it, the less I believed that was the case. Then it occurred to me that the quench plates would have only made good contact with the full thickness portions of the blade and that heat in the ground sections would have to be conducted out through the nearest point of contact with the quench plates, slowing the cooling rate near the edge.
In order to prove my theory, I'd need to do hardness testing on his knife, so I remade the knife for him and asked for it back in exchange. Sure enough, the spine is hard and the edge is softer, and by quite a bit. The picture shows hardness of 60 on the spine and as low as 51 near the edge,,, and I suspect the edge itself is softer than that. I realize that testing on non-parallel surfaces will alter the results, but in this case I think this proves my conclusion.
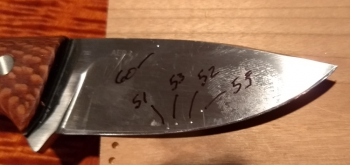
Now, this would be a moot point with and oil quenching steel, but makes a great deal of difference in this case. So, lesson learned, heat treat first for oxygen sensitive stainlesses unless you have a quenching method that is less geometry sensitive than quench plates.
-Kurt
I'd always heat treated first and ground second, except on this blade. The steel is AEBL and I heat treat with the blades in a foil pouch to prevent oxygen contact. At first, I though that maybe more oxygen had been trapped in the pouch due to the contour of the primary grinds. The more I thought about it, the less I believed that was the case. Then it occurred to me that the quench plates would have only made good contact with the full thickness portions of the blade and that heat in the ground sections would have to be conducted out through the nearest point of contact with the quench plates, slowing the cooling rate near the edge.
In order to prove my theory, I'd need to do hardness testing on his knife, so I remade the knife for him and asked for it back in exchange. Sure enough, the spine is hard and the edge is softer, and by quite a bit. The picture shows hardness of 60 on the spine and as low as 51 near the edge,,, and I suspect the edge itself is softer than that. I realize that testing on non-parallel surfaces will alter the results, but in this case I think this proves my conclusion.
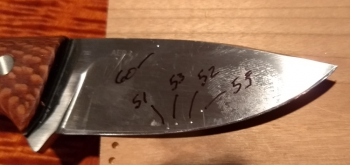
Now, this would be a moot point with and oil quenching steel, but makes a great deal of difference in this case. So, lesson learned, heat treat first for oxygen sensitive stainlesses unless you have a quenching method that is less geometry sensitive than quench plates.
-Kurt
Last edited: