Since I don't have a surface grinder, I've been using the milling machine with a 7" grinding disk to make do. While it doesn't hold near the specs of a surface grinder, it will hold a typical 10" blade within ±.003" or so. Cleans up a good bit. Just took a 5/8" stud bolt screw to disk with a jam nut to lock disk in place. Chuck up in mill, spin up to max mill speed, and feed at .005" cutting depth. Make a few passes and it tends to clean up blade side pretty good. In the image below, I put a 1/16" rod under one end to get a distal taper to blade.
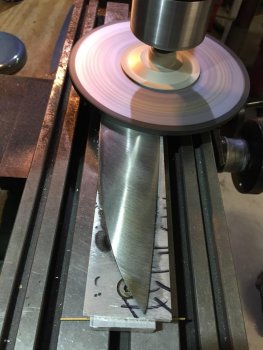
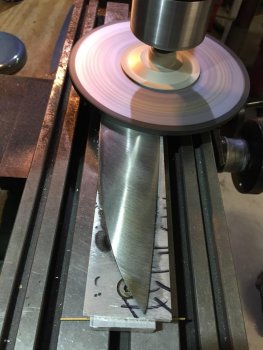