I’ll attempt to present some information on Sandvik’s alloys that are most recommended on the Sandvik site for knife blades. 12C27 and 14C28 (sometimes shown as 12C28N) are the only two I have used and I have been impressed with these. Most all this info is paraphrased from the Sandvik website, with some from personal observations and discussion with John Foster, a Sandvik technical engineer. Below is the chemical composition of 4 popular alloys. Remember, per Sandvik website: “The most important thing to remember is that hardness and corrosion resistance are related to the composition of the matrix after hardening, not the nominal chemical composition of the steel. “
Sandvik 12C27 is Sandvik’s old standby for knife steel, and has been in use for almost 50 years. It is the main steel used for knives. The current 12C27 alloy is much different and MUCH improved compared to the 1960’s era alloy due to the carbide microstructure which allows a very sharp and tough blade. While 12C27 has been Sandvik’s recommended steel for knives in the past, a new alloy 14C28 is the new alloy and I expect will become the recommended steel alloy since it has better corrosion resistance and a tad more hardness with the same toughness as 12C27. I find it interesting Sandvik chose to keep the same 12C27 designation for the steel rather than a different designation for the improved alloy. I was not able to find the chemical composition for the 1960's 12C27 alloy, so I'm not sure if the change is due to composition change, or better control of the process with modern technology.
The small size of the primary carbides gives Sandvik a decent microstructure. The maximum carbide size of Sandvik steels is 2 microns, with the average size being 0.5 microns. Per Sandvik, this is even smaller than some of the Powder steels. Take a look at this webpage for a good discussion of Sandvik’s microstructure:
www.alleima.com
In depth single piece heat treating information is provided on the Sandvik website for each of the alloys in 3 different types: no freezing, home deep freeze at -5º, and cyro-freezing at -95º, only leave piece in cold long enough to reach listed temperature. The heating soak time is the same for all alloys listed above, with only time for center of piece to stabilize at required temperature. Soak time is 5 minutes for 0.100” thick, 6 minute for 0.118, ranging up to 12 minutes for a 0.157” blade. The Quench should be as rapid as possible with maximum time is for piece to drop to 1100Fº in less than 2 minutes. This allows a profiled blade to be beveled before heat quenching and still have the edge properly hardened.
12C27 temperatures for single piece heat treating:
Freezing requires only time for material to reach desired temperature – I usually leave in freezer for an hour, bring to room temperature, then to tempering oven for 2 hours. Per the John Foster (Sandvik technical engineer) there is no advantage to tempering multiple times.
Comparing the table above to Sandvik datasheets, and different places on the website, I found a range of temperatures for the same alloy. From examining the table above the temperature difference for 12C27 and 12C27M is within the accuracy range of most ovens. John Foster said the temperatures in Sandvik's "Hardening Programs" section of website are the most current, that is where the temperatures listed in table above are from.
Below are tempering temperatures and resulting Rockwell hardness expected. The blades I’ve heat treated conform very close to published results.
12C27 single piece tempering temperatures:
14C28N single piece tempering temperatures:
From the tables above you might think 12C27 and 14C28N were almost the same, and they are - except Sandvik says the newer 14C28N has better corrosion resistance and should be a bit tougher making for a better blade.
[edited to add Aug 4th, 2014] From a VERY good authority, paraphrasing a bit: "to make folder back-springs, heat treat as normal, except temper the 14C28N at 1040 for two hours. That will get about 45 Rc without a sub zero quench, 46 -47 with a sub zero quench. A sub zero is -5ºF , no need for a long soak. You can do this in your home freezer. 14C28N makes an excellent spring if tempered correctly". I'm sure 12C27 would also.
Any typos in the above are my own typos. Any changes, comments or corrections are welcome.
Ken H>
Sandvik Alloy | Carbon % | Silicon % | Manganese % | Phosphorus % | Sulfur % | Chromium % | Nitrogen % |
12C27 | 0.6 | 0.4 | 0.4 | N/A | N/A | 13.5 | N/A |
12C27M | 0.52 | 0.4 | 0.6 | N/A | N/A | 14.5 | N/A |
13C26 | 0.68 | 0.40 | 0.60 | N/A | N/A | 12.9 | N/A |
14C28N | 0.62 | 0.2 | 0.6 | 0.025 | 0.010 | 14 | 0.11 |
Sandvik 12C27 is Sandvik’s old standby for knife steel, and has been in use for almost 50 years. It is the main steel used for knives. The current 12C27 alloy is much different and MUCH improved compared to the 1960’s era alloy due to the carbide microstructure which allows a very sharp and tough blade. While 12C27 has been Sandvik’s recommended steel for knives in the past, a new alloy 14C28 is the new alloy and I expect will become the recommended steel alloy since it has better corrosion resistance and a tad more hardness with the same toughness as 12C27. I find it interesting Sandvik chose to keep the same 12C27 designation for the steel rather than a different designation for the improved alloy. I was not able to find the chemical composition for the 1960's 12C27 alloy, so I'm not sure if the change is due to composition change, or better control of the process with modern technology.
The small size of the primary carbides gives Sandvik a decent microstructure. The maximum carbide size of Sandvik steels is 2 microns, with the average size being 0.5 microns. Per Sandvik, this is even smaller than some of the Powder steels. Take a look at this webpage for a good discussion of Sandvik’s microstructure:
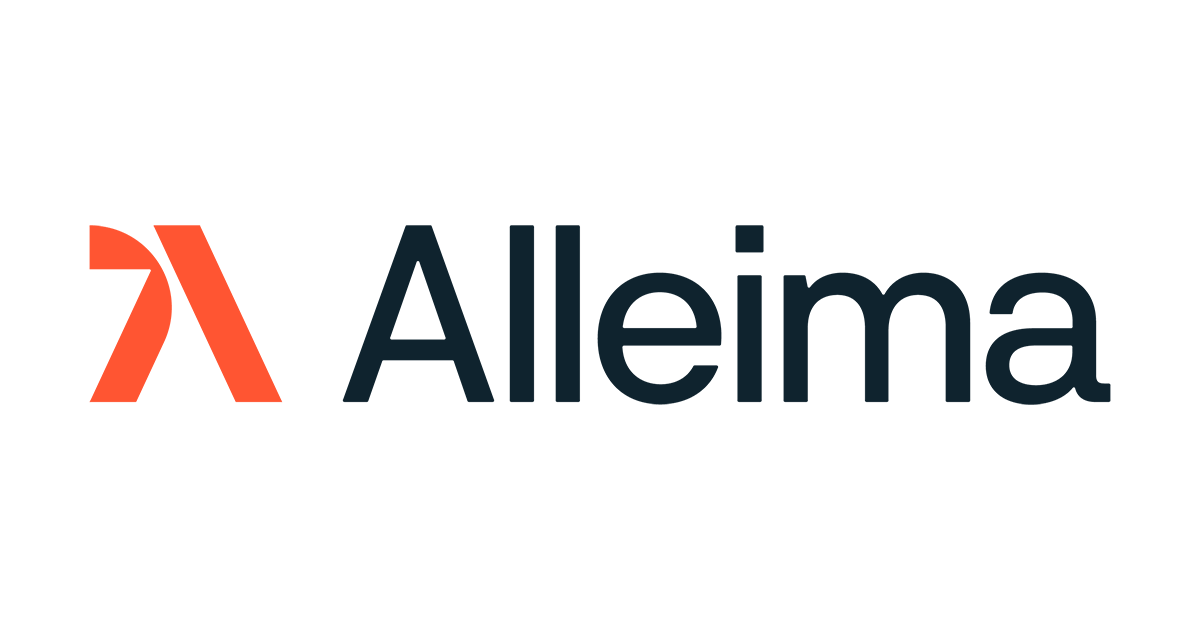
Hardening programs for Alleima knife steels
Hardening programs carefully matched to the various Alleima steel grades and to different furnace types to suit either individual pieces of knife blades or an entire batch.
In depth single piece heat treating information is provided on the Sandvik website for each of the alloys in 3 different types: no freezing, home deep freeze at -5º, and cyro-freezing at -95º, only leave piece in cold long enough to reach listed temperature. The heating soak time is the same for all alloys listed above, with only time for center of piece to stabilize at required temperature. Soak time is 5 minutes for 0.100” thick, 6 minute for 0.118, ranging up to 12 minutes for a 0.157” blade. The Quench should be as rapid as possible with maximum time is for piece to drop to 1100Fº in less than 2 minutes. This allows a profiled blade to be beveled before heat quenching and still have the edge properly hardened.
12C27 temperatures for single piece heat treating:
Method | 12C27 | 12C27M | 13C26 | 14C28N |
No Freezing | 1975ºF | 1975ºF | 1940ºF | 1920ºF |
-5º Freeze | 1995ºF | 1995ºF | N/A | 1940ºF |
-95º Freeze | 1995ºF | N/A | 1995ºF | 1975ºF |
Freezing requires only time for material to reach desired temperature – I usually leave in freezer for an hour, bring to room temperature, then to tempering oven for 2 hours. Per the John Foster (Sandvik technical engineer) there is no advantage to tempering multiple times.
Comparing the table above to Sandvik datasheets, and different places on the website, I found a range of temperatures for the same alloy. From examining the table above the temperature difference for 12C27 and 12C27M is within the accuracy range of most ovens. John Foster said the temperatures in Sandvik's "Hardening Programs" section of website are the most current, that is where the temperatures listed in table above are from.
Below are tempering temperatures and resulting Rockwell hardness expected. The blades I’ve heat treated conform very close to published results.
12C27 single piece tempering temperatures:
Temper Temp | No Freeze | -5ºF Freeze | -95ºF Freeze |
345ºF | 59 | 60 | 61 |
435ºF | 57 | 58 | 59 |
660ºF | 54 | 56 | 56 |
14C28N single piece tempering temperatures:
Temper Temp | No Freeze | -5ºF Freeze | -95ºF Freeze |
345ºF | 59 | 60 | 62 |
435ºF | 57 | 58 | 59 |
660ºF | 55 | 56 | 57 |
From the tables above you might think 12C27 and 14C28N were almost the same, and they are - except Sandvik says the newer 14C28N has better corrosion resistance and should be a bit tougher making for a better blade.
[edited to add Aug 4th, 2014] From a VERY good authority, paraphrasing a bit: "to make folder back-springs, heat treat as normal, except temper the 14C28N at 1040 for two hours. That will get about 45 Rc without a sub zero quench, 46 -47 with a sub zero quench. A sub zero is -5ºF , no need for a long soak. You can do this in your home freezer. 14C28N makes an excellent spring if tempered correctly". I'm sure 12C27 would also.
Any typos in the above are my own typos. Any changes, comments or corrections are welcome.
Ken H>
Last edited: