Bruce Bump
Forum Owner-Moderator
My friend Robin brought me an idler wheel from an army tank. Its a 24" diameter by 2 1/2" wide and has a very hard rubber tire. The rubber is bonded to steel and the steel is riveted to aluminum. I'm thinking it would be so cool to make it work. In fact its at the machine shop as we speak. They are going to make a hub for it as well as turn it to 2" and true it.
You can get an idea of its size as its sitting on a 14" wheel.
You can get an idea of its size as its sitting on a 14" wheel.
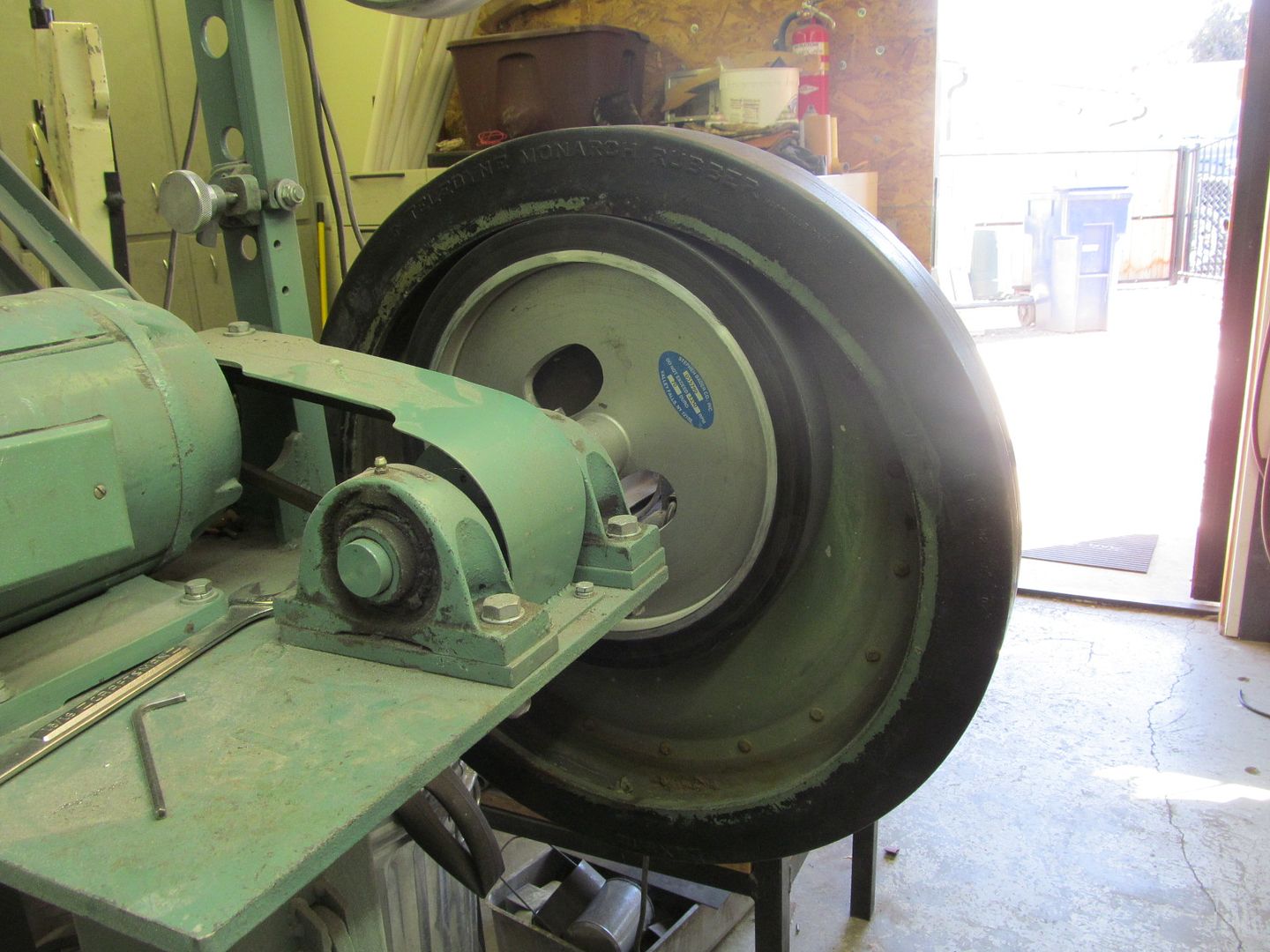
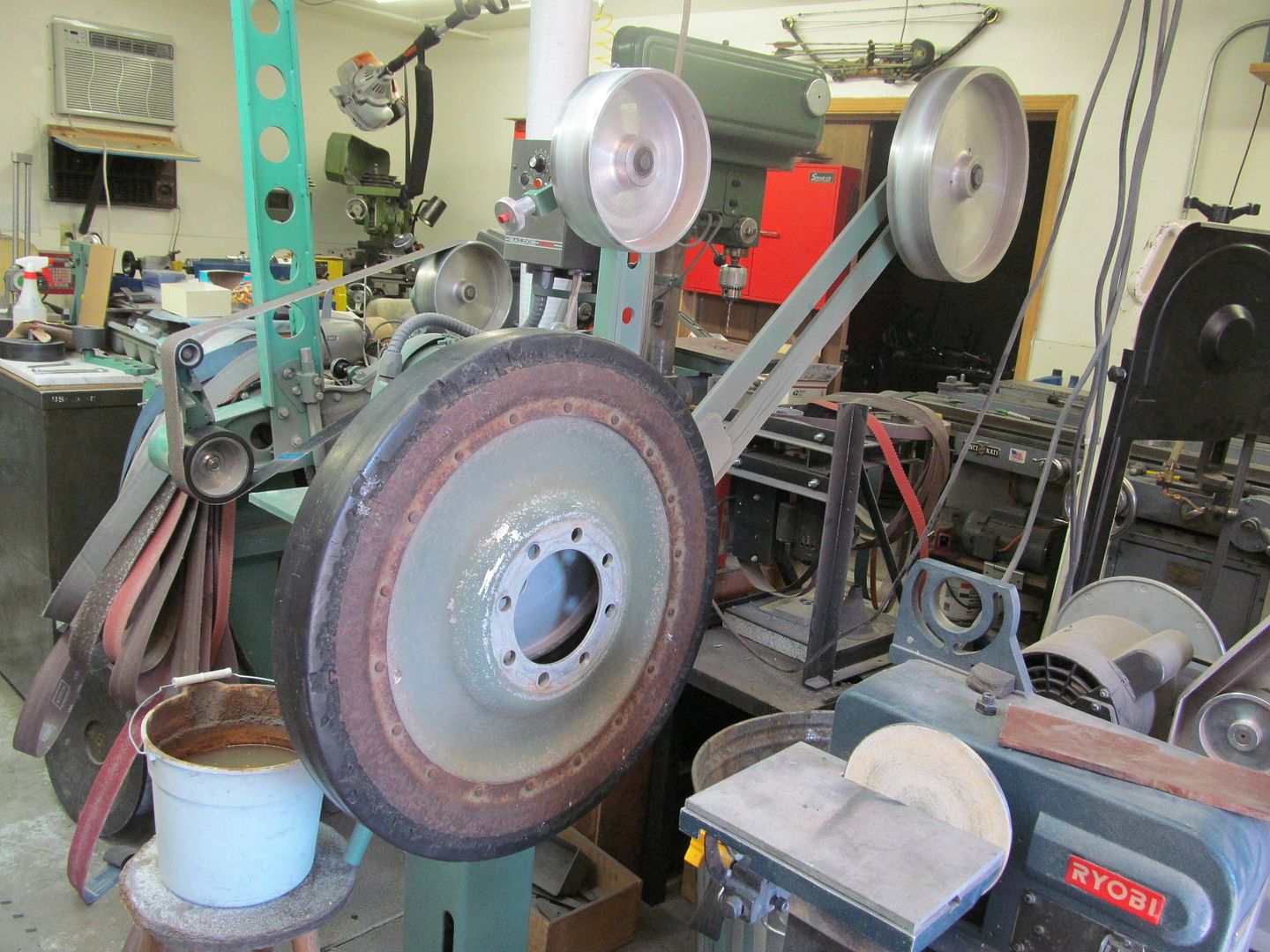