Bruce Bump
Forum Owner-Moderator
Today I reground the bevels to about 600 and started with 400 grit by hand. I use a bent spring steel pop cycle stick with sand paper strips wrapped aroung it. I can use every square inch of a sheet of sand paper this way. The 409 cleans and aids in the sanding plus it smells so nice. It is at 400 and all the vertical scratches are gone so it goes very fast from here all the way to 2000 grit.
I clamped my carbide file guide on backwards and ground the shoulders for the guard. I love this guide.
I clamped my carbide file guide on backwards and ground the shoulders for the guard. I love this guide.
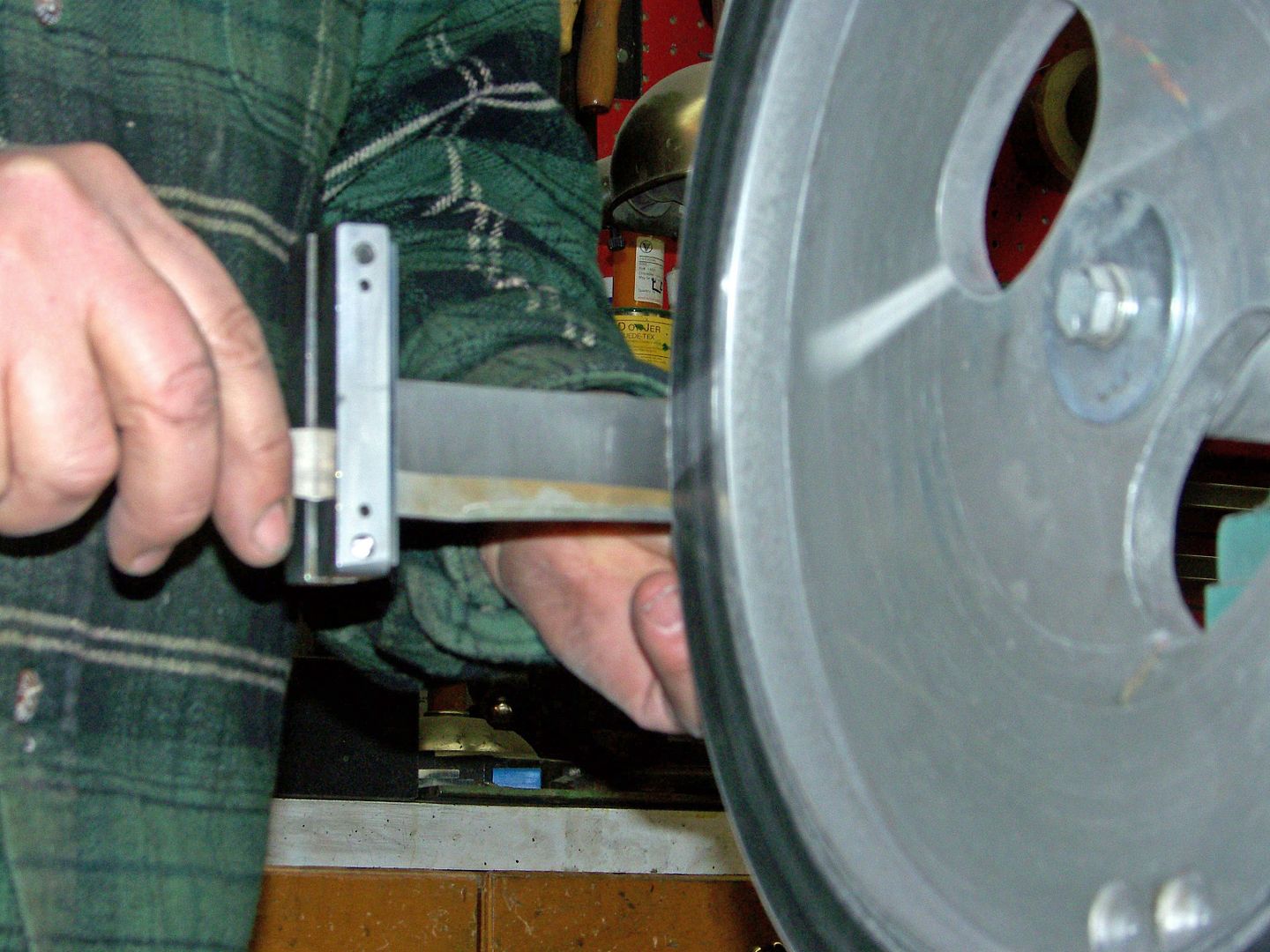
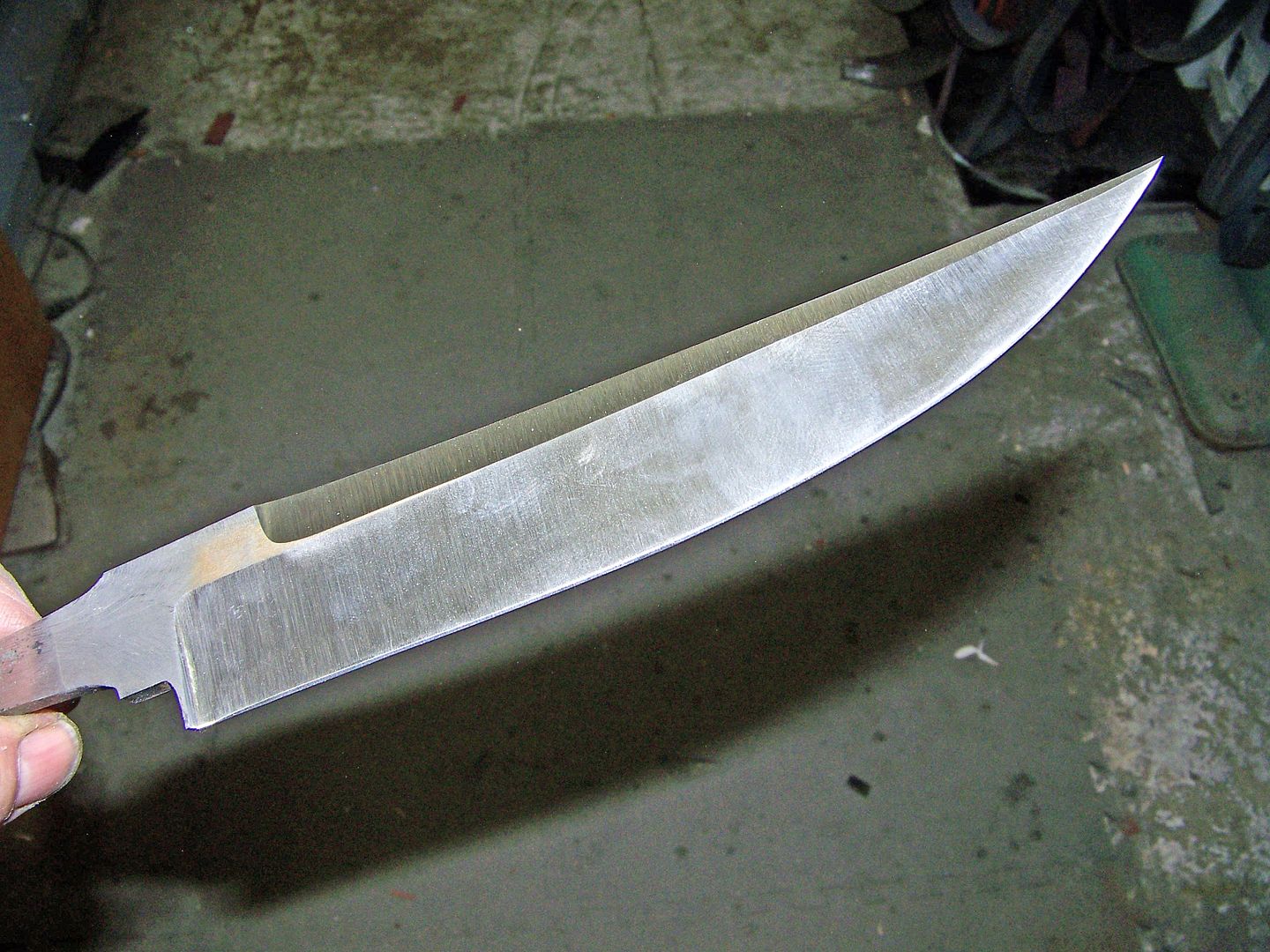
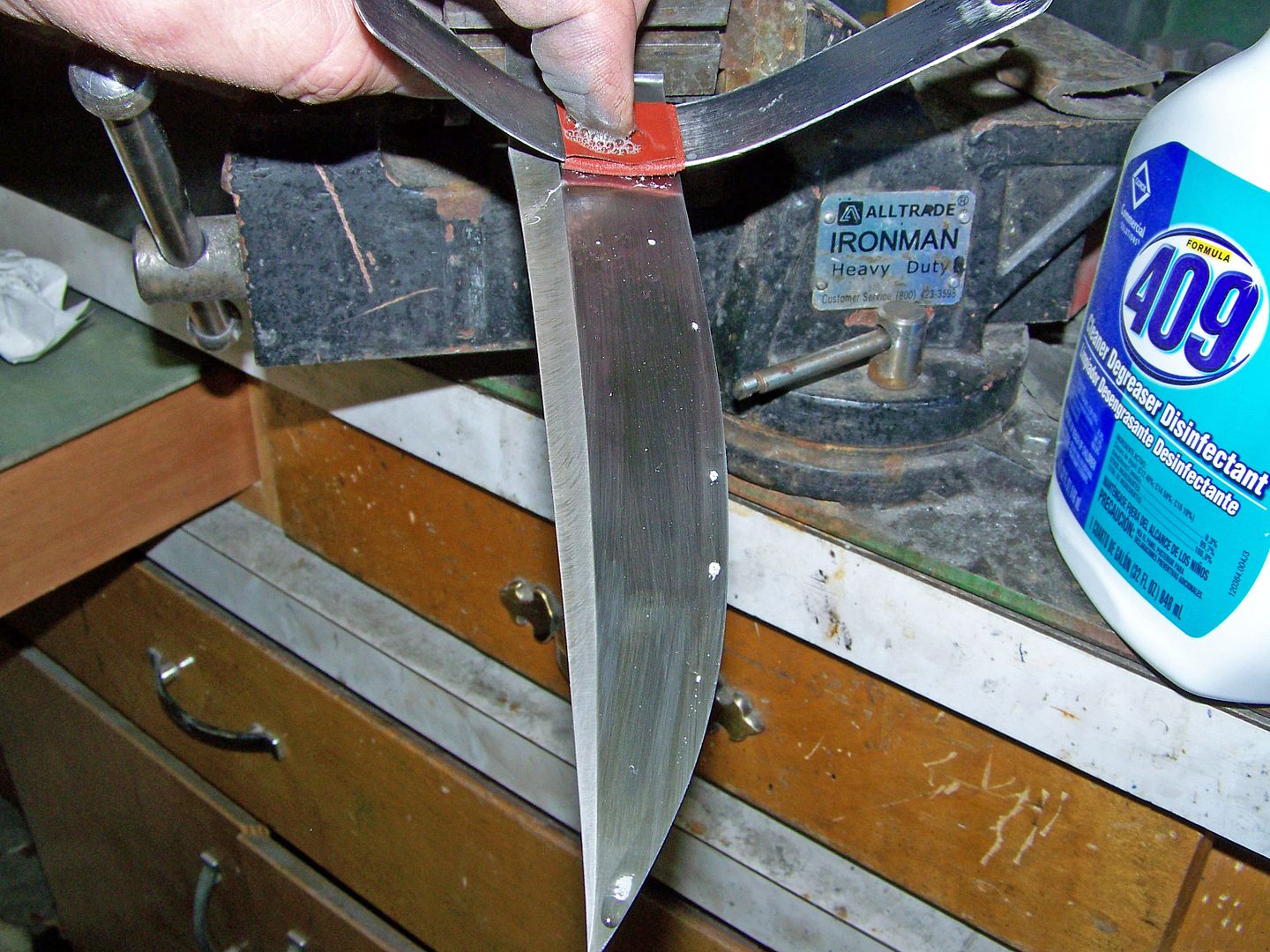
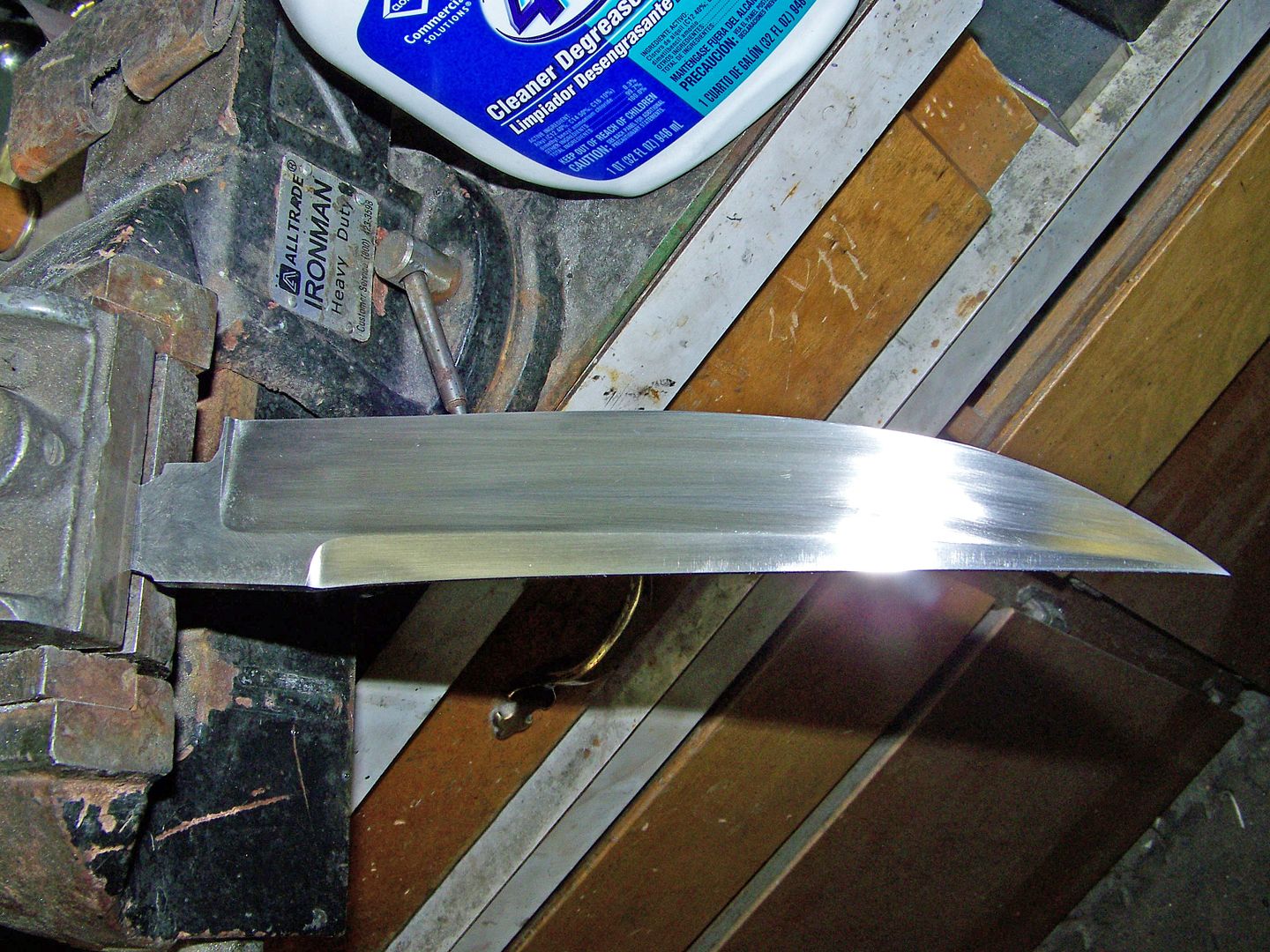
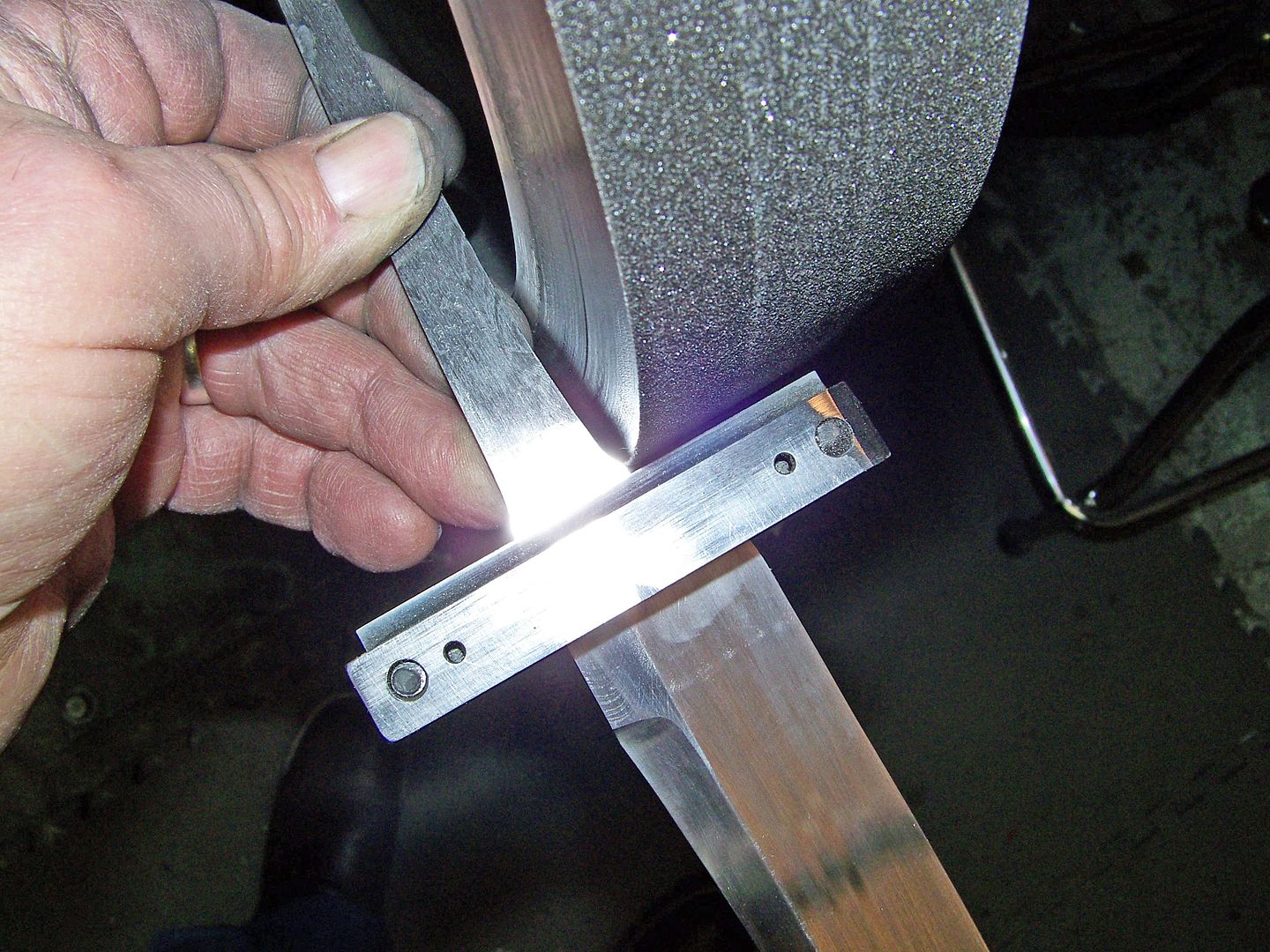
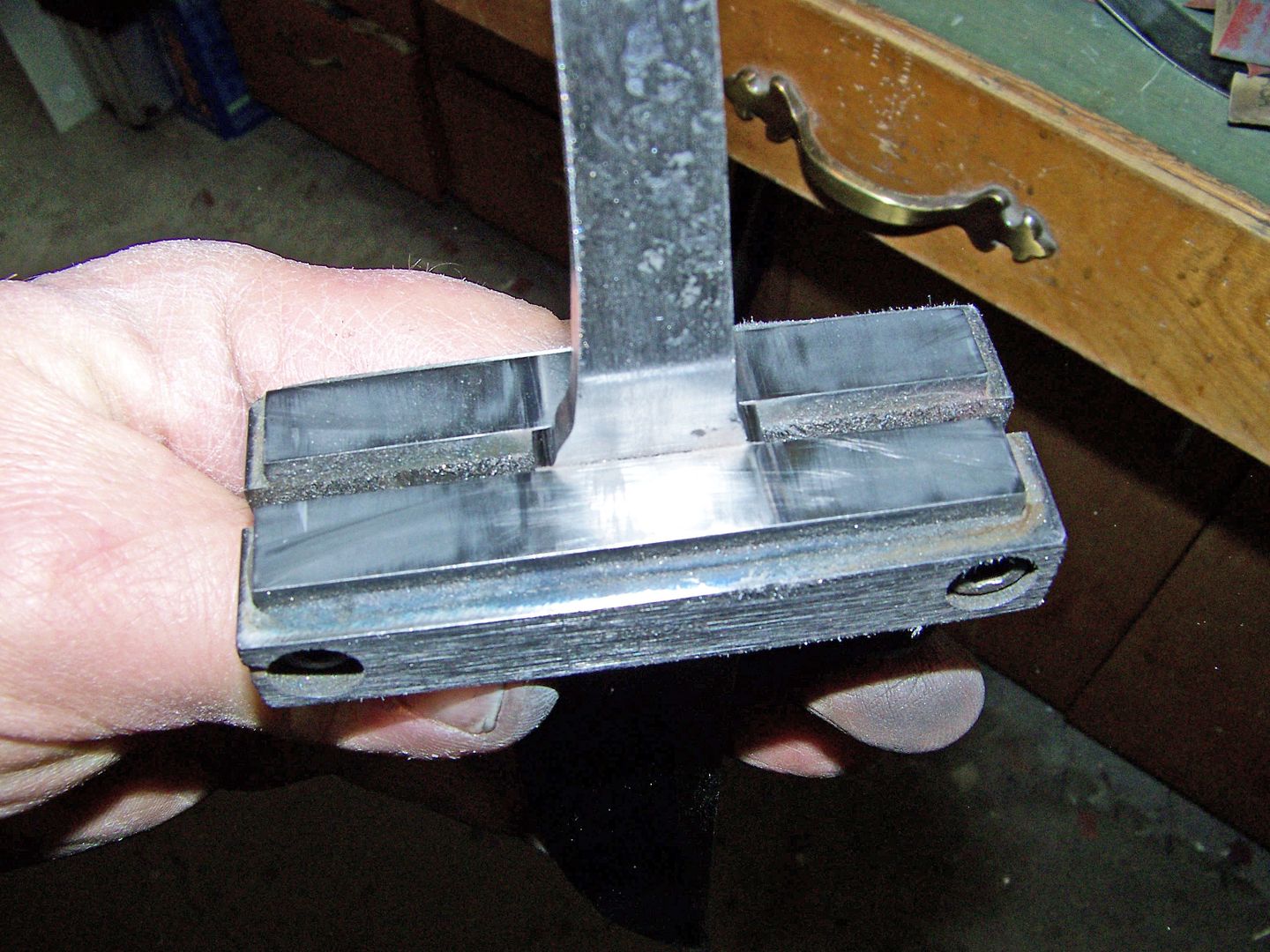